Recovery method and recovery device for valuable metals in waste miscellaneous copper electrolysis anode slime
A recovery method and technology of valuable metals, applied to the improvement of process efficiency, instruments, optics, etc., can solve the problems of complex composition of waste miscellaneous copper electrolysis anode slime, threats to the ecological environment and human health, and large fluctuations, and achieve the goal of process reagents Low consumption, high direct yield, and the effect of reducing the burden of impurity removal
- Summary
- Abstract
- Description
- Claims
- Application Information
AI Technical Summary
Problems solved by technology
Method used
Image
Examples
Embodiment 1
[0091] Put the dried materials into the rotary kiln to ventilate the air for drying and oxidative roasting, the roasting temperature is 700°C, the roasting time is 1h, and then air-cooled. The obtained calcined sand was stirred for 1 hour at a sulfuric acid concentration of 150g / L, a liquid-solid ratio of 3:1, and a temperature of 70°C, and the leaching solution and leaching slag were obtained by filtration. After analysis, the copper concentration of the leaching solution was 48g / L, and the leaching rate was 98.9%. The current density is 450A / m 2 A period of swirl electrowinning is carried out under the following conditions to obtain a copper concentration of 35g / L in the solution I after electrowinning; 2 Carry out two-stage swirl electrowinning to obtain a copper concentration of 15g / L in the electrolytic liquid II; 2 Under three-stage swirl electrowinning, the concentration of copper in solution III after electrowinning was 1.0 g / L. Distill the leaching residue at NaOH c...
Embodiment 2
[0093] Put the dried material into the rotary kiln to ventilate the air for drying and oxidative roasting, the roasting temperature is 650°C, the roasting time is 1.5h, and then air-cooled. The obtained calcined sand was stirred for 1 hour at a sulfuric acid concentration of 180g / L, a liquid-solid ratio of 2.5:1, and a temperature of 70°C, and the leaching solution and leaching residue were obtained by filtration. After analysis, the copper concentration of the leaching solution was 45g / L, and the leaching rate was 95.5%. The current density is 480A / m 2 A period of swirling electrowinning was carried out under the following conditions to obtain a copper concentration of 33g / L in the solution I after electrowinning; 2 Carry out two stages of swirl electrowinning to obtain a copper concentration of 12g / L in the electrolytic liquid II; 2 Three-stage swirl electrowinning was carried out under the following conditions, and the copper concentration of liquid III after electrowinnin...
Embodiment 3
[0095] Put the dried material into the rotary kiln to ventilate the air for drying and oxidative roasting, the roasting temperature is 600°C, the roasting time is 2.0h, and then air-cooled. The obtained calcined sand was stirred for 1 hour at a sulfuric acid concentration of 200g / L, a liquid-solid ratio of 2.5:1, and a temperature of 70°C, and the leaching solution and leaching residue were obtained by filtration. The copper concentration of the leaching solution was analyzed to be 43g / L, and the leaching rate was 91.6%. The current density is 500A / m 2 A period of swirl electrowinning is carried out under the following conditions to obtain a copper concentration of 30g / L in the solution I after electrowinning; 2 Carry out two-stage swirl electrowinning to obtain a copper concentration of 10g / L in the electrolytic liquid II; 2 Three-stage swirl electrowinning was carried out under the following conditions to obtain a copper concentration of 0.5 g / L in solution III after electr...
PUM
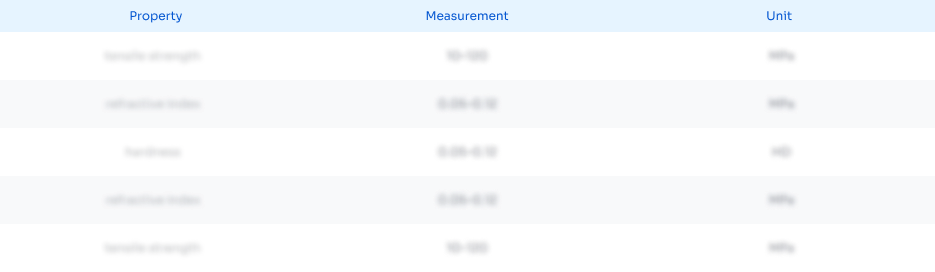
Abstract
Description
Claims
Application Information

- Generate Ideas
- Intellectual Property
- Life Sciences
- Materials
- Tech Scout
- Unparalleled Data Quality
- Higher Quality Content
- 60% Fewer Hallucinations
Browse by: Latest US Patents, China's latest patents, Technical Efficacy Thesaurus, Application Domain, Technology Topic, Popular Technical Reports.
© 2025 PatSnap. All rights reserved.Legal|Privacy policy|Modern Slavery Act Transparency Statement|Sitemap|About US| Contact US: help@patsnap.com