A kind of brake pad with low wear rate and preparation method thereof
A brake pad, low wear technology, applied in the field of brake pads, can solve the problems affecting the performance and service life of brake pads, poor wear resistance, etc., to achieve the effect of ensuring long-term effective use, low wear rate, and maintaining braking performance
- Summary
- Abstract
- Description
- Claims
- Application Information
AI Technical Summary
Problems solved by technology
Method used
Image
Examples
Embodiment 1
[0021] A brake pad with low wear rate is composed of the following parts by weight: 45 parts of high manganese steel, 18 parts of iron powder, 15 parts of carbon fiber, 8 parts of ethylene-vinyl acetate copolymer, 5 parts of lithium, potassium titanate crystal 8 parts of whisker, 6 parts of nylon powder, 14 parts of nitrile rubber powder, 3 parts of brown corundum, 4 parts of titanium dioxide, 20 parts of graphite, and 2 parts of acrylic additives containing perfluoroalkyl groups.
[0022] The preparation method of the brake pad with low wear rate comprises the following steps:
[0023] (1) Weigh high manganese steel, iron powder, lithium, nylon powder, brown corundum and graphite by weight ratio, stir evenly, add absolute ethanol as solvent, then add titanium dioxide and acrylic additive containing perfluoroalkyl group , ball milled for 9 hours, and then dried;
[0024] (2) carbon fiber, ethylene-vinyl acetate copolymer, potassium titanate whisker, nitrile rubber powder are ...
Embodiment 2
[0029] A brake pad with low wear rate is composed of the following parts by weight: 55 parts of high manganese steel, 24 parts of iron powder, 25 parts of carbon fiber, 14 parts of ethylene-vinyl acetate copolymer, 8 parts of lithium, potassium titanate crystal 12 parts of whiskers, 10 parts of nylon powder, 20 parts of nitrile rubber powder, 5 parts of brown corundum, 6 parts of zirconium silicate, 25 parts of graphite, and 4 parts of acrylic additives containing perfluoroalkyl groups.
[0030] A preparation method of a brake pad with low wear rate, comprising the following steps:
[0031] (1) Weigh high manganese steel, iron powder, lithium, nylon powder, brown corundum and graphite by weight ratio, stir evenly, add absolute ethanol as solvent, then add zirconium silicate and acrylic acid containing perfluoroalkyl group It is an additive, ball milled for 12 hours, and then dried;
[0032] (2) carbon fiber, ethylene-vinyl acetate copolymer, potassium titanate whisker, nitril...
Embodiment 3
[0037] A brake pad with low wear rate is composed of the following parts by weight: 50 parts of high manganese steel, 22 parts of iron powder, 20 parts of carbon fiber, 11 parts of ethylene-vinyl acetate copolymer, 6 parts of lithium, potassium titanate crystal 10 parts of whisker, 8 parts of nylon powder, 17 parts of nitrile rubber powder, 4 parts of brown corundum, 5 parts of alumina and barium sulfate mixture, 23 parts of graphite, and 3 parts of acrylic additives containing perfluoroalkyl groups.
[0038] A preparation method of a brake pad with low wear rate, comprising the following steps:
[0039] (1) Weigh high manganese steel, iron powder, lithium, nylon powder, brown corundum and graphite in parts by weight ratio, stir evenly, add absolute ethanol as solvent, then add alumina and barium sulfate mixture and contain perfluoroalkane based acrylic additives, ball milled for 12 hours, and then dried;
[0040] (2) carbon fiber, ethylene-vinyl acetate copolymer, potassium ...
PUM
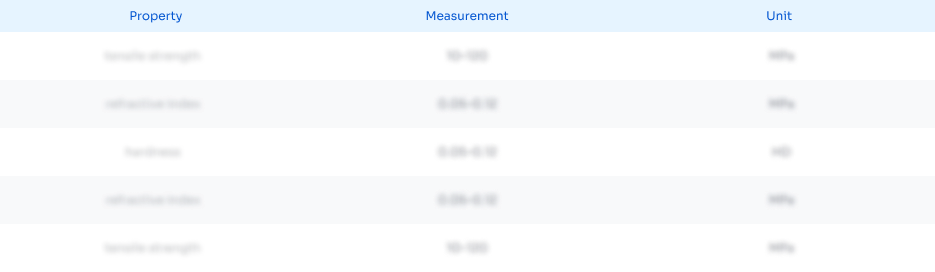
Abstract
Description
Claims
Application Information

- R&D
- Intellectual Property
- Life Sciences
- Materials
- Tech Scout
- Unparalleled Data Quality
- Higher Quality Content
- 60% Fewer Hallucinations
Browse by: Latest US Patents, China's latest patents, Technical Efficacy Thesaurus, Application Domain, Technology Topic, Popular Technical Reports.
© 2025 PatSnap. All rights reserved.Legal|Privacy policy|Modern Slavery Act Transparency Statement|Sitemap|About US| Contact US: help@patsnap.com