White photosensitive film, and preparation method and application thereof
A photosensitive film, white technology, applied in the direction of optomechanical equipment, photosensitive materials for optomechanical equipment, optics, etc.
- Summary
- Abstract
- Description
- Claims
- Application Information
AI Technical Summary
Problems solved by technology
Method used
Image
Examples
Synthetic example 1
[0080] Synthesis example 1: Synthesis of epoxy resin-(meth)acrylic resin
[0081] In a four-necked flask equipped with a stirrer, a reflux condenser, and a nitrogen tube, feed nitrogen, add 207.1 grams of epoxy resin (YDCN-704, the epoxy equivalent is 207.1) (Japan Tohto Chemical), diethylene glycol 186 grams of ether acetate, 73 grams of acrylic acid, 0.8 grams of triphenylphosphine, 0.03 grams of 4-hydroxy-2,2,6,6-tetramethylpiperidine-1-oxyl radical, after stirring into a homogeneous solution , gradually heated to 120°C, after 12 hours, 66 grams of tetrahydrophthalic anhydride was added to the reactor, then the reaction temperature was adjusted to 100°C, after stirring for 5 hours, the acid-modified epoxy- Acrylic resin, known as alkali-soluble resin 1.
Synthetic example 2
[0082] Synthesis Example 2: Synthesis of Carboxyl-containing Acrylic Resin
[0083] In a four-necked flask equipped with a stirrer, a reflux condenser, and a nitrogen tube, nitrogen gas was introduced, and 325.0 grams of diethylene glycol dimethyl ether was added, heated to 110 ° C, and then 204.0 grams of methacrylic acid and benzyl acrylate were added. 81.0 grams, 77.0 grams of methyl methacrylate, 302.0 grams of solvent propylene glycol methyl ether acetate, and the mixture of 12.0 grams of synthetic catalyst peroxide 1,1-dimethylethyl-2-ethyl peroxyhexanoate , drop it into the system uniformly in about 3 hours, then keep it at 110°C for 3 hours, wait for the deactivation of the peroxide, and obtain the polymer. After the resin is cooled, add 289.0 grams of Nantong Xinnaxi S-100 , 3.0 grams of phosphorus triphenylide, and 0.08 grams of polymerization inhibitor 4-hydroxy-2,2,6,6-tetramethylpiperidine-1-oxyl free radicals were added, the temperature was raised to 100 ° C, and...
Synthetic example 3
[0084] Synthesis Example 3: Synthesis of Modified Polyimide
[0085]In a four-neck flask equipped with a stirrer, a reflux condenser, and a nitrogen tube, feed nitrogen, add 25.0 grams (0.1 moles) of xylylmethane 4,4-diisocyanate, and 15.0 grams of γ-butyrolactone, and stir Evenly, add polycarbonate diol (product of Asahi Kasei Co., Ltd., PCDL T5651) 50.0 grams (0.05 moles), dimethylolpropionic acid 3.3 grams (0.025 moles) and γ-butyrolactone 30 grams, for this The solution was heated to 80° C., and after 10 hours, a uniform and transparent polymer liquid was obtained. Then add 4,4-biphenyl ether dianhydride 15.5g (0.05 moles) and γ-butyrolactone 30.0 grams in this solution, adjust the reaction temperature to 160 ℃ of heating for 2 hours, become uniform light yellow-brown solution, later Lower the temperature in the kettle to 100°C, then add 6.5 grams (0.05 moles) of hydroxyethyl methacrylate and 6.7 grams of γ-butyrolactone to the reaction system, keep stirring at a temperat...
PUM
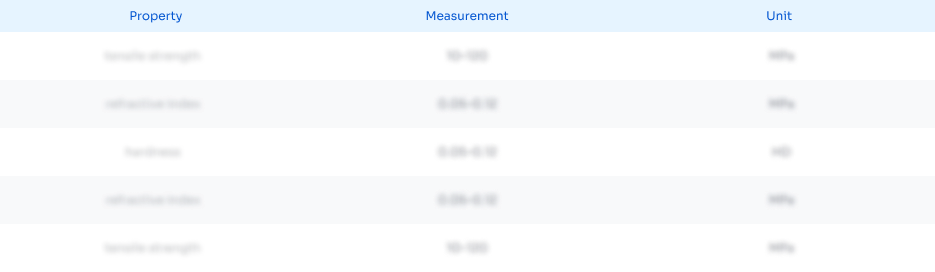
Abstract
Description
Claims
Application Information

- R&D
- Intellectual Property
- Life Sciences
- Materials
- Tech Scout
- Unparalleled Data Quality
- Higher Quality Content
- 60% Fewer Hallucinations
Browse by: Latest US Patents, China's latest patents, Technical Efficacy Thesaurus, Application Domain, Technology Topic, Popular Technical Reports.
© 2025 PatSnap. All rights reserved.Legal|Privacy policy|Modern Slavery Act Transparency Statement|Sitemap|About US| Contact US: help@patsnap.com