Nylon wool top dyeing process capable of improving nylon spinning operation conditions
A technology of running condition and nylon, which is applied in the field of nylon top dyeing process, can solve the problems of low production efficiency, poor running condition, and easy adhesion of nylon fiber to the top roller, etc., so as to improve production efficiency, improve running condition and improve adhesion effect of effect
- Summary
- Abstract
- Description
- Claims
- Application Information
AI Technical Summary
Problems solved by technology
Method used
Image
Examples
Embodiment 1
[0027] A kind of nylon top dyeing process that can improve running condition in this embodiment comprises the following steps:
[0028] Step 1: wool top dyeing, reload the nylon wool ball into the dye vat, add penetration enhancer, acetic acid, leveling agent at room temperature, run for 10 minutes, then add dye, run for 10 minutes, then raise the temperature to 98 at 0.5°C / min ℃, keep warm for 45 minutes, then cool down to 80 ℃, drain. Wherein said penetration enhancer is ALBAFLOW FFW, and its consumption is 0.5mL / L; Described acetic acid consumption is 0.749%; Described leveling agent is ALBEGAL SET, and its consumption is 1mL / L; Described dyestuff is LANASET metal Complex dyes, and its dosage is 1.34%.
[0029] Step 2: Pickling the tops at high temperature, adding acetic acid, adjusting the pH value to 5.6, raising the temperature to 100°C and keeping it warm for 30 minutes, cooling down to 80°C, and draining.
[0030] Step 3: Pickling the tops at high temperature, adding...
Embodiment 2
[0033] A kind of nylon top dyeing process that can improve running condition in this embodiment comprises the following steps:
[0034] Step 1: wool top dyeing, reload the nylon wool ball into the dye vat, add penetration enhancer, acetic acid, leveling agent at room temperature, run for 10 minutes, then add dye, run for 10 minutes, then raise the temperature to 98 at 0.5°C / min ℃, keep warm for 60 minutes, then cool down to 80 ℃, drain. Wherein said penetration enhancer is ALBAFLOW FFW, and its consumption is 0.5mL / L; Described acetic acid consumption is 2.07%; Described leveling agent is ALBEGAL SET, and its consumption is 1mL / L; Described dyestuff is ISOLAN acid Dye, and its consumption is 3.7%.
[0035] Step 2: Soaping, add soaping agent at room temperature, run for 10 minutes, then raise the temperature to 60°C and keep it warm for 30 minutes, then drain. Described soaping agent is DEKOL SN-S, and its consumption is 1mL / L.
[0036] Step 3: Color fixing, add color fixing...
PUM
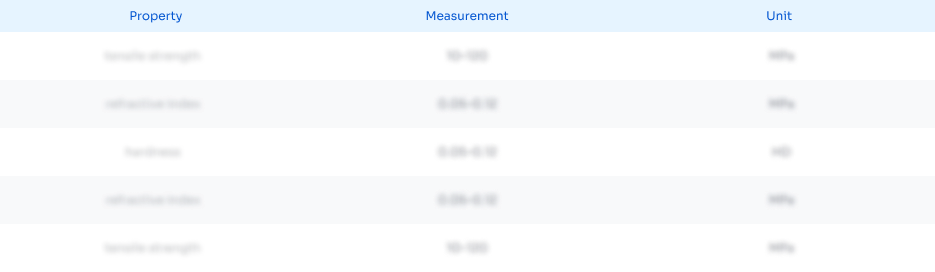
Abstract
Description
Claims
Application Information

- Generate Ideas
- Intellectual Property
- Life Sciences
- Materials
- Tech Scout
- Unparalleled Data Quality
- Higher Quality Content
- 60% Fewer Hallucinations
Browse by: Latest US Patents, China's latest patents, Technical Efficacy Thesaurus, Application Domain, Technology Topic, Popular Technical Reports.
© 2025 PatSnap. All rights reserved.Legal|Privacy policy|Modern Slavery Act Transparency Statement|Sitemap|About US| Contact US: help@patsnap.com