Modified ABS material and preparation method thereof
A technology of ABS material and ABS resin, which is applied in the field of polymers, can solve problems such as poor comprehensive physical and mechanical properties, failure to meet market demand, poor impact resistance, etc., and achieve improved melt fluidity, improved dispersion uniformity, and swelling good effect
- Summary
- Abstract
- Description
- Claims
- Application Information
AI Technical Summary
Problems solved by technology
Method used
Image
Examples
Embodiment 1
[0026] A modified ABS material, by mass percentage, its preparation raw materials include the following components: 50% ABS resin, 16.1% ASA resin, 10.7% ultra-high molecular weight polyethylene, 13.2% styrene, 3.5% poly Phenyl ether, 4% styrene grafted maleic anhydride copolymer, 2.5% ethylene bis-stearamide.
[0027] A method for preparing modified ABS material includes the following steps:
[0028] (1) Vacuum dry the ABS resin and ASA resin at 80°C for 8 hours; dry the polyphenylene ether in vacuum at 120°C for 3 hours;
[0029] (2) Add ultra-high molecular weight polyethylene and xylene at a mass ratio of 1:9 into a vacuum reactor and mix them evenly, and then swell at 100°C for 30 minutes to obtain an ultra-high molecular weight polyethylene initial swelling liquid;
[0030] (3) Add excess ethanol to the initial swelling liquid of ultra-high molecular weight polyethylene and filter to obtain the initial swelling ultra-high molecular weight polyethylene, and then add ethylene bis-...
Embodiment 2
[0035] A modified ABS material, in terms of mass percentage, its preparation raw materials include the following components: 63% ABS resin, 10.3% ASA resin, 6% ultra-high molecular weight polyethylene, 11% styrene, 1.7% poly Phenyl ether, 7% styrene grafted maleic anhydride copolymer, 1% ethylene bis-stearamide.
[0036] A method for preparing a modified ABS material, according to the above formula and using the preparation method in Example 1 to prepare a modified ABS material. The difference is that the extrusion temperature of the twin-screw extruder is 205°C.
Embodiment 3
[0038] A modified ABS material, in terms of mass percentage, its preparation raw materials include the following components: 70% ABS resin, 8% ASA resin, 8.5% ultra-high molecular weight polyethylene, 7% styrene, 2% poly Phenyl ether, 3% styrene grafted maleic anhydride copolymer, 1.5% ethylene bis-stearamide.
[0039] A method for preparing a modified ABS material, according to the above formula and using the preparation method in Example 1 to prepare a modified ABS material. The difference is that the extrusion temperature of the twin-screw extruder is 215°C.
PUM
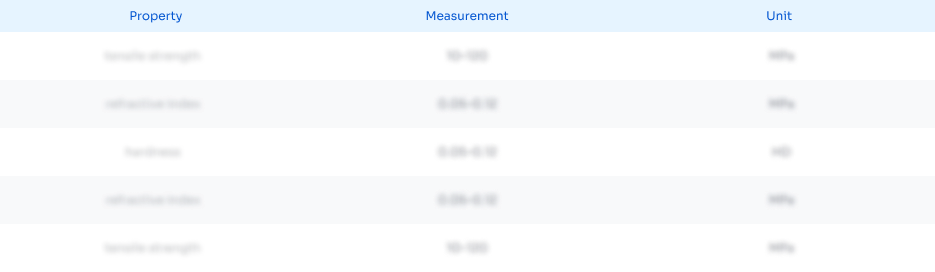
Abstract
Description
Claims
Application Information

- R&D
- Intellectual Property
- Life Sciences
- Materials
- Tech Scout
- Unparalleled Data Quality
- Higher Quality Content
- 60% Fewer Hallucinations
Browse by: Latest US Patents, China's latest patents, Technical Efficacy Thesaurus, Application Domain, Technology Topic, Popular Technical Reports.
© 2025 PatSnap. All rights reserved.Legal|Privacy policy|Modern Slavery Act Transparency Statement|Sitemap|About US| Contact US: help@patsnap.com