Composite steel quenching process
A composite steel and process technology, applied in the direction of quenching device, improvement of process efficiency, manufacturing tools, etc., can solve the problems of non-continuous quenching operation and increased processing difficulty, and achieve the goal of lowering temperature, reducing production cost and improving collection efficiency Effect
- Summary
- Abstract
- Description
- Claims
- Application Information
AI Technical Summary
Problems solved by technology
Method used
Image
Examples
Embodiment approach
[0038] As an embodiment of the present invention, an airbag 18 is fixedly installed between the cutter block 17 and the cylinder 16; a water spray hole 171 is provided on the cutter block 17; the airbag 18 and the water spray hole 171 is connected, and a one-way valve is installed at the communicating place; a water pipe 181 is installed on the airbag 18; the end of the water pipe 181 is located below the liquid level of the quenching liquid in the quenching tank 1; the water pipe 181 is installed Has a one-way valve;
[0039] When working, when the cutter block 17 starts to cut the steel bar, the airbag 18 installed between the cutter block 17 and the cylinder 16 expands, and the airbag 18 absorbs the quenching from the quenching box 1 through the installed water pipe 181 After the cutting block 17 completes the cutting work and returns to the original position, the airbag 18 is squeezed so that the quenching liquid absorbed in the airbag 18 is sprayed from the water set on the ...
PUM
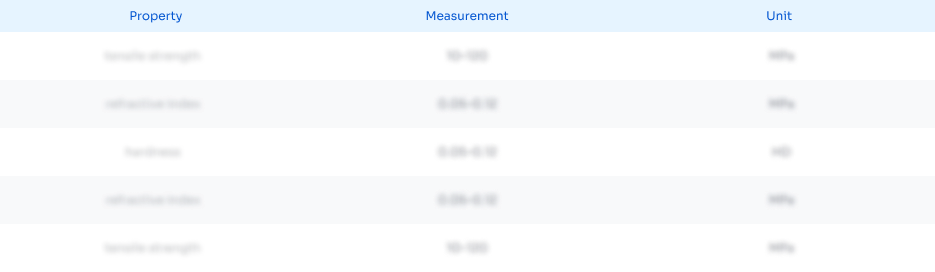
Abstract
Description
Claims
Application Information

- R&D Engineer
- R&D Manager
- IP Professional
- Industry Leading Data Capabilities
- Powerful AI technology
- Patent DNA Extraction
Browse by: Latest US Patents, China's latest patents, Technical Efficacy Thesaurus, Application Domain, Technology Topic, Popular Technical Reports.
© 2024 PatSnap. All rights reserved.Legal|Privacy policy|Modern Slavery Act Transparency Statement|Sitemap|About US| Contact US: help@patsnap.com