A method for sulfur gas reduction of gypsum to produce sulphoaluminate cement and co-production of sulfuric acid
A technology for producing sulphoaluminate and sulfur, which is applied in cement production, chemical instruments and methods, sulfur compounds, etc., can solve the problem of low decomposition rate of gypsum, achieve fast and efficient decomposition reaction, and save resources
- Summary
- Abstract
- Description
- Claims
- Application Information
AI Technical Summary
Problems solved by technology
Method used
Image
Examples
preparation example Construction
[0083] F. Preparation of cement
[0084] Sulphoaluminate cement products with different performance requirements are obtained by adding gypsum and composite materials to the cement clinker from the cooler in step E, and then undergoing subsequent grinding processing.
Embodiment 1
[0087] process such as figure 2 As shown, desulfurized gypsum and high-grade bauxite are used as raw materials. The raw materials are dried and ground to >95%-80μm, and most of the fly ash produced by the combustion of fuel coal in the rotary kiln enters the clinker. The chemical composition is shown in Table 1.
[0088] Table 1 Chemical composition of raw materials and raw meal
[0089]
[0090]
[0091] The above-mentioned desulfurized gypsum dihydrate and high-grade bauxite raw materials are composed in parts by mass: 76.1 parts of desulfurized gypsum dihydrate and 23.9 parts of high-grade bauxite are mixed evenly, and the raw materials are mixed evenly after drying and grinding. The obtained raw meal is metered and sent to C 1a The gas inlet of the cyclone preheater (in this embodiment, the multi-stage suspension preheating system includes 4 stages of cyclone preheaters, where C 1a is the topmost cyclone preheater), and the SO-containing 2 The hot gas is subjected...
Embodiment 2
[0101] process such as image 3 As shown, desulfurized gypsum, bauxite, fly ash, and iron slag are used as raw materials, and the raw materials are dried and ground to >95%-80μm, and most of the fly ash produced by the combustion of fuel coal in the rotary kiln enters the clinker , The chemical composition of raw materials and raw meal is shown in Table 4.
[0102] Table 4 Chemical Composition of Raw Materials and Raw Meals
[0103] project CaO SiO 2
al 2 o 3
Fe 2 o 3
MgO TiO 2
Na 2 o
SO 3
LOSS total Desulfurization gypsum 34.35 1.56 1.78 1.15 2.24 0.12 0.15 41.56 17.06 99.97 Bauxite 1.50 14.54 72.34 3.37 0.07 0.66 0.24 0.13 6.98 99.83 fly ash 1.48 43.50 35.38 1.92 0.70 1.18 0.33 0.68 14.77 99.94 iron slag 40.46 12.24 1.93 27.64 4.74 0.00 0.00 2.98 9.86 99.85 Raw material 28.19 7.02 13.33 3.40 2.03 0.26 0.16 30.51 15.10 100.00
[0104] The a...
PUM
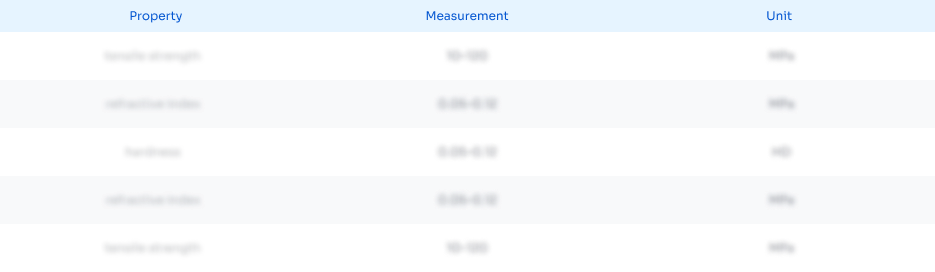
Abstract
Description
Claims
Application Information

- R&D
- Intellectual Property
- Life Sciences
- Materials
- Tech Scout
- Unparalleled Data Quality
- Higher Quality Content
- 60% Fewer Hallucinations
Browse by: Latest US Patents, China's latest patents, Technical Efficacy Thesaurus, Application Domain, Technology Topic, Popular Technical Reports.
© 2025 PatSnap. All rights reserved.Legal|Privacy policy|Modern Slavery Act Transparency Statement|Sitemap|About US| Contact US: help@patsnap.com