Alloy smelting furnace
A smelting furnace and alloy technology, which is applied in the field of alloy smelting furnaces, can solve problems such as metals are prone to safety hazards, reduce alloy smelting speed, and unfavorable production of enterprises, and achieve the effects of increasing speed, improving safety, and avoiding dumping of the furnace body
- Summary
- Abstract
- Description
- Claims
- Application Information
AI Technical Summary
Problems solved by technology
Method used
Image
Examples
Embodiment Construction
[0030] The following will clearly and completely describe the technical solutions in the embodiments of the present invention with reference to the accompanying drawings in the embodiments of the present invention. Obviously, the described embodiments are only some, not all, embodiments of the present invention. Based on the embodiments of the present invention, all other embodiments obtained by persons of ordinary skill in the art without creative efforts fall within the protection scope of the present invention.
[0031] see Figure 1-6 , the present invention provides a technical solution: an alloy smelting furnace, including a HY-25AB model high-frequency induction heating machine 1 and a furnace body 2, and the right side wall of the high-frequency induction heating machine 1 is fixedly connected with a 6ED1052-1FB08-0BA0 model control 3, the output terminal of the controller 3 is electrically connected to the input terminal of the high-frequency induction heating machine...
PUM
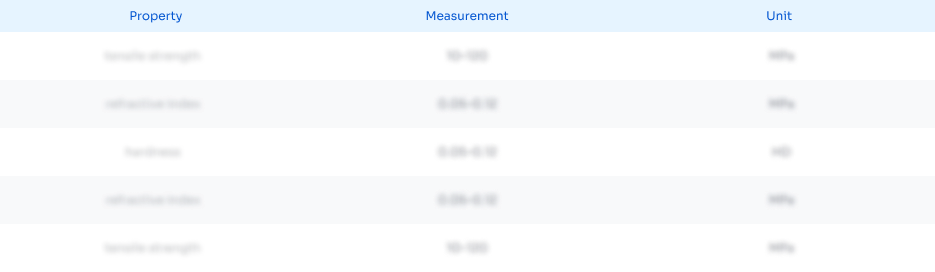
Abstract
Description
Claims
Application Information

- R&D
- Intellectual Property
- Life Sciences
- Materials
- Tech Scout
- Unparalleled Data Quality
- Higher Quality Content
- 60% Fewer Hallucinations
Browse by: Latest US Patents, China's latest patents, Technical Efficacy Thesaurus, Application Domain, Technology Topic, Popular Technical Reports.
© 2025 PatSnap. All rights reserved.Legal|Privacy policy|Modern Slavery Act Transparency Statement|Sitemap|About US| Contact US: help@patsnap.com