A kind of etching method of ultra-high pressure etching foil
A technology of corroding foil and ultra-high pressure, which is applied in the field of electrolytic corrosion technology, can solve the problems of easy blockage of corrosion holes and small corrosion holes of anode foil, and achieve the effect of increasing the density of pores, increasing the diameter of holes, and increasing the density of pitting corrosion
- Summary
- Abstract
- Description
- Claims
- Application Information
AI Technical Summary
Problems solved by technology
Method used
Image
Examples
Embodiment 1
[0030] Primary pretreatment: use a mixture of 28wt% sulfuric acid and 4wt% hydrochloric acid, the temperature is 45°C, and the treatment time is controlled at 20 seconds.
[0031] Secondary pretreatment: use a mixture of 28wt% sulfuric acid and 4wt% hydrochloric acid, add 0.08g / L ferric chloride, the temperature is 55°C, and the AC frequency is 50HZ, 0.1A / cm 2 , 5s for initial pitting treatment.
[0032] Primary corrosion: use a mixture of 35 wt% sulfuric acid and 9 wt% hydrochloric acid, the temperature is 70 °C, and the intermittent pulse power-on mode is used for 7 times for electrolytic corrosion, and the power is cut off for 6 times. 8s, using direct current. Pulse power-on mode: first power on for 6s to attenuate the current density from 1.4A / cm2 to 0.6A / cm2, and then power on for 12s to attenuate the current density from 0.6A / cm2 to 0.02A / cm2.
[0033] Secondary corrosion: The corrosion solution is 9 wt% nitric acid and 0.1 g / L sodium polystyrene sulfonate, the temper...
Embodiment 2
[0036] Primary pretreatment: use a mixture of 30wt% sulfuric acid and 6wt% hydrochloric acid, the temperature is 45°C, and the treatment time is controlled at 20 seconds.
[0037] Secondary pretreatment: use a mixture of 30wt% sulfuric acid and 6wt% hydrochloric acid, add 0.06g / L ferric chloride, the temperature is 55℃, and the initial pitting corrosion treatment is carried out with an alternating current frequency of 80HZ, 0.06A / cm2, and 8s .
[0038] Primary corrosion: use a mixture of 35 wt% sulfuric acid and 9 wt% hydrochloric acid, the temperature is 70 °C, and the intermittent pulse power-on mode is used for 7 times for electrolytic corrosion, and the power is cut off for 6 times. 8s, using direct current. Pulse power-on mode: first power on for 7s to attenuate the current density from 1.3A / cm2 to 0.7A / cm2, and then power on for 11s to attenuate the current density from 0.7A / cm2 to 0.02A / cm2.
[0039] Secondary corrosion: The corrosion solution is 9 wt% nitric acid and...
Embodiment 3
[0042] Primary pretreatment: use a mixture of 28wt% sulfuric acid and 4wt% hydrochloric acid, the temperature is 45°C, and the treatment time is controlled at 20 seconds.
[0043] Secondary pretreatment: use 28wt% sulfuric acid and 4 wt% hydrochloric acid mixture, add 0.08g / L ferric chloride, the temperature is 55℃, and the initial pitting corrosion treatment is carried out with an alternating current frequency of 80HZ, 0.06A / cm2, 8s .
[0044] Primary corrosion: use a mixture of 35 wt% sulfuric acid and 9 wt% hydrochloric acid, the temperature is 70 °C, and the intermittent pulse power-on mode is used for 7 times for electrolytic corrosion, and the power is cut off for 6 times. 8s, using direct current. Pulse electrification mode: first add 8s to attenuate the current density from 1.3A / cm2 to 0.6A / cm2, and then charge for 10s to attenuate the current density from 0.6A / cm2 to 0.02A / cm2.
[0045] Secondary corrosion: The corrosion solution is 9 wt% nitric acid and 0.1 g / L sod...
PUM
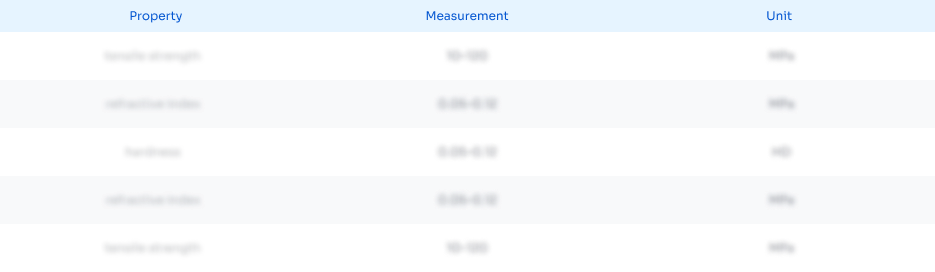
Abstract
Description
Claims
Application Information

- R&D
- Intellectual Property
- Life Sciences
- Materials
- Tech Scout
- Unparalleled Data Quality
- Higher Quality Content
- 60% Fewer Hallucinations
Browse by: Latest US Patents, China's latest patents, Technical Efficacy Thesaurus, Application Domain, Technology Topic, Popular Technical Reports.
© 2025 PatSnap. All rights reserved.Legal|Privacy policy|Modern Slavery Act Transparency Statement|Sitemap|About US| Contact US: help@patsnap.com