Method for preparing hydro-demetalization catalyst for heavy oil
A heavy oil hydrogenation and catalyst technology, which is applied in the direction of metal/metal oxide/metal hydroxide catalyst, catalyst carrier, chemical instrument and method, etc., can solve the problem of reducing catalyst activity and activity stability, catalyst pore size distribution dispersion, carrier Problems such as pore distribution and dispersion, to achieve the effect of controlling product properties, easy to grasp, and simple operation
- Summary
- Abstract
- Description
- Claims
- Application Information
AI Technical Summary
Problems solved by technology
Method used
Image
Examples
example 1
[0028]Get pseudo-boehmite dry rubber powder (produced by Shenyang Catalyst Factory, alumina dry basis weight content 65%), every 100g of pseudo-boehmite dry rubber powder is added with 2 g of squid powder, and mix evenly; For diaspore dry rubber powder, dissolve 3g of glucose and 1.5g of phosphoric acid in 80mL of distilled water, and mix the resulting solution with the above materials evenly. Extrude into a clover-shaped strip with a diameter of 1.8mm on a screw extruder, dry it at 120°C for 3 hours, bake the dried molding at a temperature of 450°C for 2 hours, and then bake it at a temperature of 650°C for 3 hours , to obtain the alumina carrier B1 provided by the present invention.
example 2
[0030] Same as Example 1, except that glucose is changed to sucrose, the addition amount is 5g per 100g of pseudo-boehmite dry rubber powder, and the addition of phosphoric acid is 1.0g per 100g of pseudo-boehmite dry rubber powder. Calcined at a temperature of 1.5 hours, and then calcined at a temperature of 700° C. for 2 hours to obtain the alumina carrier B2 provided by the present invention.
example 3
[0032] Same as Example 1, except that the addition of glucose is 6g per 100g of pseudo-boehmite dry rubber powder, the addition of phosphoric acid is 0.8g per 100g of pseudo-boehmite dry rubber powder, and the molding is roasted at a temperature of 500°C for 1.5 hours, and then calcined at a temperature of 650° C. for 2.5 hours to obtain the alumina carrier B3 provided by the present invention.
PUM
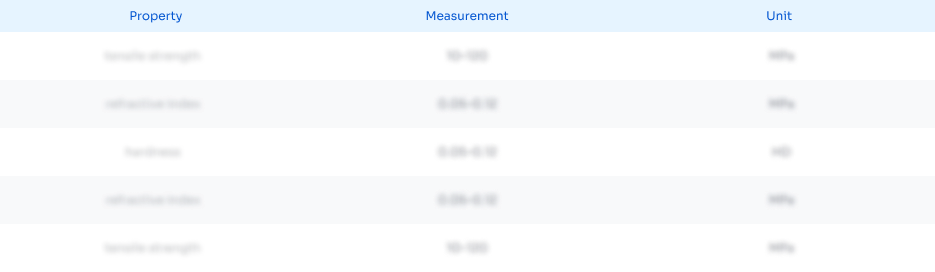
Abstract
Description
Claims
Application Information

- R&D
- Intellectual Property
- Life Sciences
- Materials
- Tech Scout
- Unparalleled Data Quality
- Higher Quality Content
- 60% Fewer Hallucinations
Browse by: Latest US Patents, China's latest patents, Technical Efficacy Thesaurus, Application Domain, Technology Topic, Popular Technical Reports.
© 2025 PatSnap. All rights reserved.Legal|Privacy policy|Modern Slavery Act Transparency Statement|Sitemap|About US| Contact US: help@patsnap.com