Multi-layer rotating disc thin-layer chemical reactor and using method thereof
A rotating disk and reactor technology, applied in chemical instruments and methods, chemical/physical/physicochemical stationary reactors, separation methods, etc., can solve problems such as insufficient mixing reactions, facilitate processing, and enhance mass transfer rate , the effect of reducing the pressure drop
- Summary
- Abstract
- Description
- Claims
- Application Information
AI Technical Summary
Problems solved by technology
Method used
Image
Examples
Embodiment 1
[0052] First prepare stock solution, CuSO 4 ·5H 2 O and Fe 2 (SO 4 ) 3 Dissolved in deionized water to obtain a concentration of Cu 2+ =1.0 g / l, Fe 3+ =3.0 g / l aqueous solution, adjust its pH value to 1.8 with sulfuric acid; at the same time, use Lix985 copper extractant and sulfonated kerosene to obtain an organic phase with a volume fraction of 20%. Equipment parameters: single-layer rotating disk reactor, the angle of the 4 inner rotating disks is 10°, the diameter of the 4 inner rotating disks is 300mm, and the distance between the two disks is 10mm.
[0053] Test conditions: the rotation speed of the inner turntable 4 is 350r / min; the flow rate of the organic phase is 1200mL / min, the flow rate of the aqueous phase is 580mL / min, and the temperature is 20°C.
[0054] Test results: ICP was used to analyze the content of copper ions and iron ions in the raffinate, and the extraction rate of copper was calculated to be 99.9%, while iron ions were hardly extracted into th...
Embodiment 2
[0056] First prepare the stock solution, the In 2 (SO 4 ) 3 , ZnSO 4 ·7H 2 O and Fe 2 (SO 4 ) 3 Dissolved in deionized water to obtain a concentration of In 2+ =1.0 g / L, Zn3+=3.0g / L, Fe 3+ =5.0 g / L aqueous solution, adjust its pH value to 1.8 with sulfuric acid; at the same time, use P204 extractant and sulfonated kerosene to obtain an organic phase with a volume fraction of 30%. Equipment parameters: three-layer rotating disk reactor, the angle of the 4 inner rotating disks is 90°, the diameter of the 4 inner rotating disks is 1m, and the distance between the two disks is 5mm.
[0057] Test conditions: the rotation speed of the inner turntable 4 is 500r / min; the flow rate of the organic phase is 10L / min, the flow rate of the aqueous phase is 5L / min, and the temperature is 20°C.
[0058] Test results: ICP was used to analyze the content of copper ions and iron ions in the raffinate, and the calculated extraction rate of In was 99.9%, the extraction rate of iron ions w...
Embodiment 3
[0060] A pilot test of denitrification was carried out for the flue gas produced in an iron ore sintering workshop after dust removal and desulfurization, and the absorption liquid was prepared as 0.05mol / L NaOH and 0.05mol / LH 2 o 2 100m 3 ;
[0061] Equipment parameters: object-layer rotating disk reactor, the angle of the 4 inner rotating disks is 90°, the diameter of the 4 inner rotating disks is 1.5 m, and the distance between the two disks is 15 mm.
[0062] Test conditions: the speed of the inner turntable 4 is 600r / min; the NOx flow rate is 1200m 3 / h The flow rate of the water phase of the absorption liquid is 5L / min, the two phases are contacted and mixed in countercurrent, the temperature is about 30°C, and the test is continued for 24h.
[0063] The test results are: the average NOx absorption efficiency can reach more than 90%, the average NOx content before the denitrification operation is 830ppm, and the average NOx content in the flue gas is lower than 50ppm...
PUM
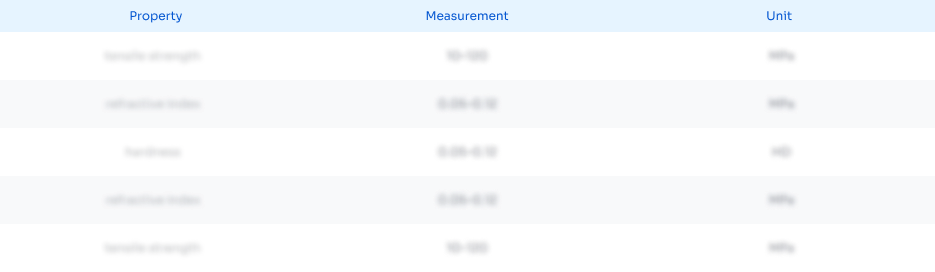
Abstract
Description
Claims
Application Information

- Generate Ideas
- Intellectual Property
- Life Sciences
- Materials
- Tech Scout
- Unparalleled Data Quality
- Higher Quality Content
- 60% Fewer Hallucinations
Browse by: Latest US Patents, China's latest patents, Technical Efficacy Thesaurus, Application Domain, Technology Topic, Popular Technical Reports.
© 2025 PatSnap. All rights reserved.Legal|Privacy policy|Modern Slavery Act Transparency Statement|Sitemap|About US| Contact US: help@patsnap.com