Integral dioxin removal catalyst and preparation method thereof
A monolithic, catalyst technology, applied in chemical instruments and methods, physical/chemical process catalysts, separation methods, etc., can solve the problem of unsuitable industrial high-flow flue gas, small number of honeycomb monomer pores, poisoning of precious metal catalysts, etc. problem, to achieve good reaction efficiency, good anti-poisoning effect, and the effect of increasing adhesion
- Summary
- Abstract
- Description
- Claims
- Application Information
AI Technical Summary
Problems solved by technology
Method used
Image
Examples
Embodiment 1
[0019] Embodiment 1, the preparation of catalyst of the present invention
[0020] Dissolve 71.26g of oxalic acid in 1500g of water, then add 45.29g of ammonium metavanadate, and heat at 80°C to dissolve ammonium metavanadate to obtain vanadium oxalate solution; dissolve 67.93g of ammonium paratungstate in 2500g of water, add 1080g of TiO 2 , then add the aforementioned vanadium oxalate solution, 96g NH 4 HCO 3 and 90g of silica sol-alumina sol mixture (Si / Al=2), stirred for 6 hours to obtain a catalyst coating slurry.
[0021] Part of the catalyst coating slurry was dried at 110° C. for 12 hours and calcined at 550° C. for 4 hours to obtain a powder catalyst.
[0022] A 200-mesh honeycomb ceramic carrier of 100×100×200 mm was immersed in the catalyst coating slurry for 5 minutes and then taken out, and the excess slurry in the carrier was removed by blowing with compressed air, then dried at 110°C for 12 hours, and then calcined at 550°C for 4 hours. A monolithic catalyst ...
Embodiment 2
[0032] Embodiment 2, the preparation of catalyst of the present invention
[0033] Dissolve 17.82g oxalic acid in 375g water, then add 11.51g ammonium metavanadate, heat at 80°C to dissolve ammonium metavanadate, and prepare vanadium oxalate solution; dissolve 20.72g ammonium paratungstate in 2025g water, add 570g TiO 2 , then add the aforementioned vanadium oxalate solution, 18g NH 4 HCO 3 and 30 g of aluminum-modified silica sol (Si / Al=3), stirred for 6 hours to prepare a catalyst coating slurry.
[0034] A 200-mesh Φ84.5×60mm honeycomb ceramic carrier was immersed in the catalyst coating slurry for 5 minutes and then taken out, and the excess slurry in the carrier was removed by blowing with compressed air, then dried at 110°C for 12 hours, and then calcined at 550°C for 4 hours. A monolithic catalyst is produced. The coating amount of the catalyst coating is 15% of the weight of the honeycomb ceramic carrier, and the mass percentage of each component in the catalyst coa...
Embodiment 3
[0035] Embodiment 3, the preparation of catalyst of the present invention
[0036] Dissolve 70.42g of oxalic acid in 1500g of water, then add 45.22g of ammonium metavanadate, heat at 80°C to dissolve ammonium metavanadate, and obtain vanadium oxalate solution; dissolve 48.87g of ammonium paratungstate in 1500g of water, add 504g of TiO 2 , then add the aforementioned vanadium oxalate solution, 60g NH 4 HCO 3 and 15g of silica sol-alumina sol mixture (Si / Al=1), stirred for 6 hours to prepare catalyst coating slurry.
[0037] A 200-mesh Φ84.5×60mm honeycomb ceramic carrier was immersed in the catalyst coating slurry for 5 minutes and then taken out, and the excess slurry in the carrier was removed by blowing with compressed air, then dried at 110°C for 12 hours, and then calcined at 550°C for 4 hours. A monolithic catalyst is produced. The coating amount of the catalyst coating is 5% of the weight of the honeycomb ceramic carrier, and the mass percentage of each component in ...
PUM
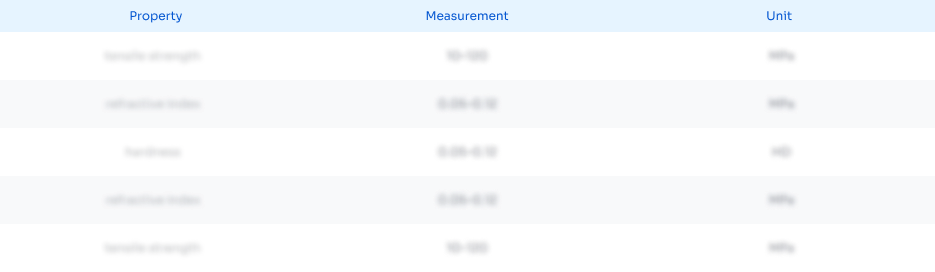
Abstract
Description
Claims
Application Information

- R&D
- Intellectual Property
- Life Sciences
- Materials
- Tech Scout
- Unparalleled Data Quality
- Higher Quality Content
- 60% Fewer Hallucinations
Browse by: Latest US Patents, China's latest patents, Technical Efficacy Thesaurus, Application Domain, Technology Topic, Popular Technical Reports.
© 2025 PatSnap. All rights reserved.Legal|Privacy policy|Modern Slavery Act Transparency Statement|Sitemap|About US| Contact US: help@patsnap.com