Single-component mirror ink and preparation method thereof
A mirror ink, one-component technology, applied in the field of ink, can solve the problems of mirror ink, such as poor weather resistance, moisture resistance, water boiling resistance, ink loss of mirror effect and metallic luster, non-recyclable recycling, etc., to achieve excellent water boiling performance, The effect of shortening the baking time and reducing the phenomenon of dust adsorption
- Summary
- Abstract
- Description
- Claims
- Application Information
AI Technical Summary
Problems solved by technology
Method used
Image
Examples
Embodiment 1
[0043]A single-component mirror ink, its raw materials include: varnish 70%, vacuum electroplating aluminum silver paste 30%;
[0044] The varnish includes by weight percentage: cellulose acetate butyrate 35%, benzomelamine formaldehyde resin 5%, hexamethylene diisocyanate 8%, medium active carboxylate 0.5%, aminosilane coupling agent 4%, polyacrylic acid Ester 1%, DBE 30%, PMA 16.5%.
Embodiment 2
[0046] A one-component mirror ink, the raw materials of which include 50% of varnish and 50% of vacuum electroplating aluminum-silver paste by weight percentage;
[0047] The varnish includes by weight percentage: cellulose acetate butyrate 40%, butylated melamine formaldehyde resin 6%, hexamethylene diisocyanate 6%, medium active carboxylate 0.2%, epoxy silane coupling agent 5% , polymer acrylate 2%, DBE20%, PMA16.8%
Embodiment 3
[0049] A one-component mirror ink, the raw materials of which include 60% of varnish and 40% of vacuum electroplating aluminum silver paste by weight percentage;
[0050] Varnish comprises by weight percentage: nitrocellulose: 35%, benzomelamine formaldehyde resin 4%, alicyclic isophorone diisocyanate 6.6%, mixed metal carboxylate 0.4%, aminosilane coupling agent 3%, Leveling agent 1%, DBE30%, PMA20%.
PUM
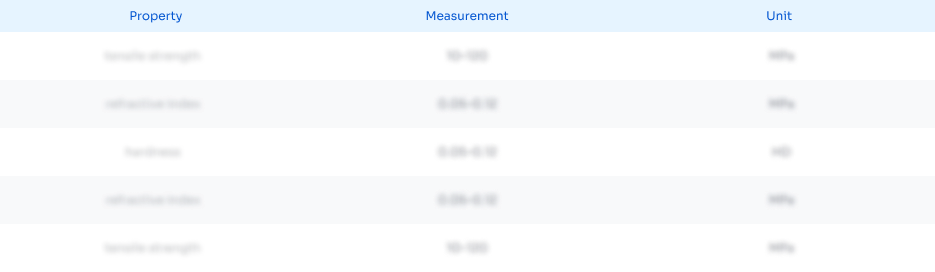
Abstract
Description
Claims
Application Information

- R&D
- Intellectual Property
- Life Sciences
- Materials
- Tech Scout
- Unparalleled Data Quality
- Higher Quality Content
- 60% Fewer Hallucinations
Browse by: Latest US Patents, China's latest patents, Technical Efficacy Thesaurus, Application Domain, Technology Topic, Popular Technical Reports.
© 2025 PatSnap. All rights reserved.Legal|Privacy policy|Modern Slavery Act Transparency Statement|Sitemap|About US| Contact US: help@patsnap.com