A plate condenser with intermediate draining
A condenser and plate type technology is applied in the field of plate type condensers to achieve the effects of increasing the phase change heat transfer coefficient, simplifying the design of the flow channel, and having a simple and compact device structure.
- Summary
- Abstract
- Description
- Claims
- Application Information
AI Technical Summary
Problems solved by technology
Method used
Image
Examples
Embodiment Construction
[0027] In order to make the above objects, features and advantages of the present invention more comprehensible, the present invention will be further described in detail below in conjunction with the accompanying drawings and specific embodiments.
[0028] like Figure 1 to Figure 5 As shown, a plate condenser capable of draining liquid in the middle of this embodiment is mainly composed of an upper box body 1, a lower box body 2, a side sealing plate 3, an A-type heat exchange plate 4, a B-type heat exchange plate 5 and a middle Drainage pipe 6 forms. All parts can be made of plates and pipes through die stamping and welding processes, and the parts are connected together by brazing. The specific processing technology is the same as that of the current corrugated plate heat exchanger and will not be described in detail.
[0029] In this embodiment, 4 A-type heat exchange plates 4 and 5 B-type heat exchange plates 5 are alternately arranged to form 8 flow channels, of which ...
PUM
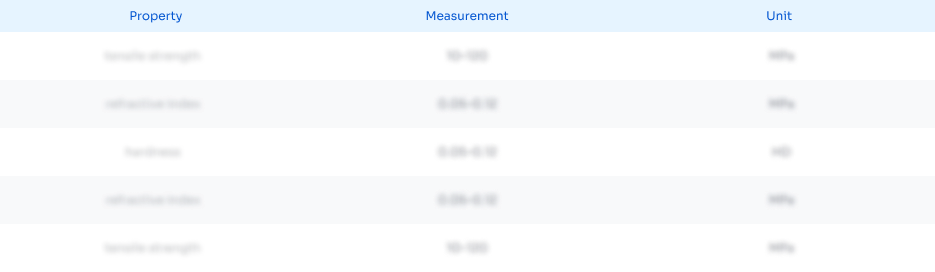
Abstract
Description
Claims
Application Information

- Generate Ideas
- Intellectual Property
- Life Sciences
- Materials
- Tech Scout
- Unparalleled Data Quality
- Higher Quality Content
- 60% Fewer Hallucinations
Browse by: Latest US Patents, China's latest patents, Technical Efficacy Thesaurus, Application Domain, Technology Topic, Popular Technical Reports.
© 2025 PatSnap. All rights reserved.Legal|Privacy policy|Modern Slavery Act Transparency Statement|Sitemap|About US| Contact US: help@patsnap.com