A kind of magnesium-air battery anode material and preparation method thereof
A technology for air batteries and anode materials, applied in the direction of battery electrodes, fuel cell half-cells and secondary battery-type half-cells, circuits, etc., can solve the problem of reducing battery efficiency, reducing battery discharge voltage, reducing surface active areas, etc. problems, to achieve the effect of optimizing the discharge process, excellent discharge performance, and reducing the thickness of the accumulation
- Summary
- Abstract
- Description
- Claims
- Application Information
AI Technical Summary
Problems solved by technology
Method used
Image
Examples
Embodiment 1
[0025] A magnesium-air battery anode material, the mass composition percentage of the anode material: Zn 2.0wt.%, Ca 0.1wt.%, the rest is magnesium.
[0026] (1) Take by weighing commercial pure magnesium (99.95wt.%), pure zinc (98.5wt.%), Mg-9.4wt.% according to the above-mentioned content Zn 2.0wt.%, Ca 0.1wt.%. %Ca intermediate alloy, and remove the oxide skin on the surface;
[0027] (2) Put the pure magnesium in (1) into a clean cast iron crucible and put them together in the hearth of a resistance furnace, preheat at 150°C for 20min to remove the moisture in the crucible, pure zinc and Mg-9.4wt. The %Ca master alloy is put into another clean cast iron crucible and put into another electric resistance furnace hearth, and is kept at a constant temperature of 300°C for standby;
[0028] (3) Raise the temperature of the resistance furnace with pure magnesium in (2) to 700°C, and feed a volume ratio of 19:1 (N 2 :SF 6 ) protective gas, when the melt temperature reaches 720...
Embodiment 2
[0031] A magnesium-air battery anode material, the mass composition percentage of the anode material: Zn 2.0wt.%, Ca 0.2wt.%, the rest is magnesium.
[0032] (1) Take by weighing commercial pure magnesium (99.95wt.%), pure zinc (98.5wt.%), Mg-9.4wt.% according to the above-mentioned content Zn 2.0wt.%, Ca 0.2wt.%. %Ca intermediate alloy, and remove the oxide skin on the surface;
[0033] (2) Put the pure magnesium in (1) into a clean cast iron crucible and put them together in the hearth of a resistance furnace, preheat at 200°C for 15min to remove the moisture in the crucible, pure zinc and Mg-9.4wt. The %Ca master alloy is put into another clean cast iron crucible and put into another electric resistance furnace hearth, and is kept at a constant temperature of 300°C for standby;
[0034] (3) Raise the temperature of the resistance furnace with pure magnesium in (2) to 710°C, and feed a volume ratio of 19:1 (N 2 :SF 6 ) protective gas, when the melt temperature reaches 725...
Embodiment 3
[0037]A magnesium-air battery anode material, the mass composition percentage of the anode material: Zn 2.0wt.%, Ca 0.5wt.%, the rest is magnesium.
[0038] (1) Take by weighing commercial pure magnesium (99.95wt.%), pure zinc (98.5wt.%), Mg-9.4wt.% according to the above-mentioned content Zn 2.0wt.%, Ca 0.5wt.%. %Ca intermediate alloy, and remove the oxide skin on the surface;
[0039] (2) Put the pure magnesium in (1) into a clean cast iron crucible and put them together in the hearth of a resistance furnace, preheat at 250°C for 15min to remove the moisture in the crucible, pure zinc and Mg-9.4wt. The %Ca master alloy is put into another clean cast iron crucible and put into another electric resistance furnace hearth, and is kept at a constant temperature of 300°C for standby;
[0040] (3) Raise the temperature of the resistance furnace with pure magnesium in (2) to 713°C, and feed a volume ratio of 19:1 (N 2 :SF 6 ) protective gas, when the melt temperature reaches 728°...
PUM
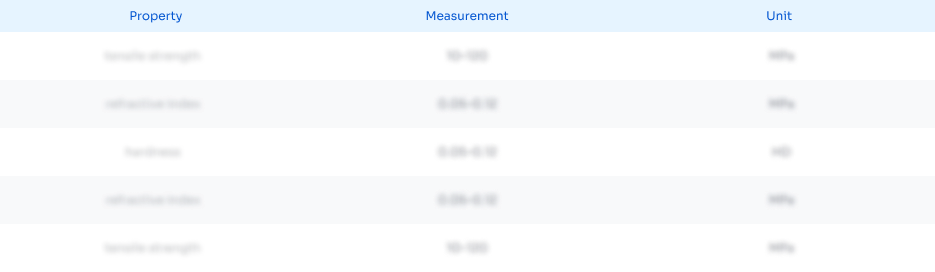
Abstract
Description
Claims
Application Information

- R&D Engineer
- R&D Manager
- IP Professional
- Industry Leading Data Capabilities
- Powerful AI technology
- Patent DNA Extraction
Browse by: Latest US Patents, China's latest patents, Technical Efficacy Thesaurus, Application Domain, Technology Topic, Popular Technical Reports.
© 2024 PatSnap. All rights reserved.Legal|Privacy policy|Modern Slavery Act Transparency Statement|Sitemap|About US| Contact US: help@patsnap.com