High-performance trapezoidal aluminum alloy material and production method thereof
A technology of aluminum alloy materials and production methods, which is applied in the direction of metal processing equipment, mechanical cleaning, manufacturing tools, etc., can solve the problems of reducing the strength and service life of the hub, uneven composition and performance, and coarse grains of finished products. Uniform and delicate, less impurities, uniform composition effect
- Summary
- Abstract
- Description
- Claims
- Application Information
AI Technical Summary
Problems solved by technology
Method used
Examples
Embodiment 1
[0047] Example 1: A high-performance trapezoidal aluminum alloy material, its composition by weight percentage is: silicon Si 7.4%, iron Fe≤0.12%, copper Cu 0.42, magnesium Mg 0.4%, titanium Ti 0.1%, total impurity content < 0.02%, the balance is aluminum.
[0048] The production method of above-mentioned high-performance trapezoidal aluminum alloy material, its steps are as follows:
[0049]A. First add the cold material of the same composition, the addition amount is 15-20% of the furnace capacity, and then add the electrolytic aluminum liquid ingredients, Fe≤0.07% and Si≤0.04% in the electrolytic aluminum liquid, turn on the electromagnetic stirring and heat up at the same time, let the cold material melt To achieve a mixed melt with uniform composition;
[0050] B. When the temperature reaches above 750°C, sprinkle a certain amount of slagging agent, turn on the electromagnetic stirring for 30 to 40 minutes, and then perform slag removal on the surface of the aluminum liq...
Embodiment 2
[0070] Embodiment 2: The production method of this embodiment is basically the same as that of Embodiment 1, and the similarities will not be repeated. The difference is: a high-performance trapezoidal aluminum alloy material, and its composition is by weight percentage: silicon Si 7.5% , iron Fe ≤0.12%, copper Cu 0.46, magnesium Mg 0.45%, titanium Ti 0.15%, total impurity content <0.02%, and the balance is aluminum.
Embodiment 3
[0071] Embodiment 3: The production method of this embodiment is basically the same as that of Embodiment 1, and the similarities will not be repeated. The difference is: a high-performance trapezoidal aluminum alloy material, and its composition is by weight percentage: silicon Si 7.4~ 7.5%, iron Fe ≤0.12%, copper Cu 0.42-0.46, magnesium Mg 0.4-0.45%, titanium Ti 0.1-0.15%, total impurity content <0.02%, and the balance is aluminum.
PUM
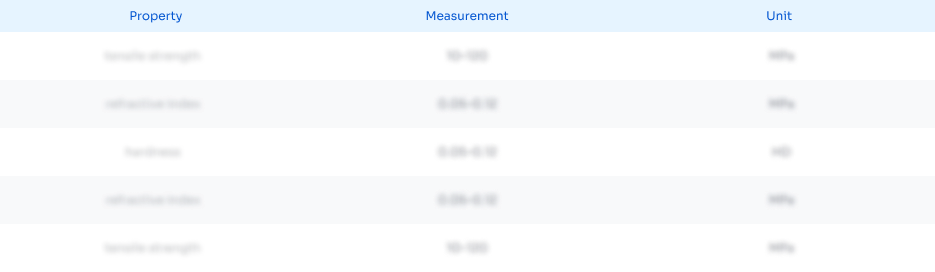
Abstract
Description
Claims
Application Information

- R&D Engineer
- R&D Manager
- IP Professional
- Industry Leading Data Capabilities
- Powerful AI technology
- Patent DNA Extraction
Browse by: Latest US Patents, China's latest patents, Technical Efficacy Thesaurus, Application Domain, Technology Topic, Popular Technical Reports.
© 2024 PatSnap. All rights reserved.Legal|Privacy policy|Modern Slavery Act Transparency Statement|Sitemap|About US| Contact US: help@patsnap.com