Modified Fenton-like catalyst and preparation method and application thereof
A catalyst and modification technology, applied in the field of modified Fenton-like catalysts and preparation, can solve the problems of complex and discontinuous application process, low catalytic degradation rate, loss of active components, etc., and achieve high hydrogen peroxide utilization, strong Tolerance and stability, long life effect
- Summary
- Abstract
- Description
- Claims
- Application Information
AI Technical Summary
Problems solved by technology
Method used
Examples
Embodiment 1
[0032] (1) Add 500 mL of deionized water and 16.45 g of Co(NO 3 ) 2 ·6H 2 O and 21.21g of Al(NO 3 ) 3 9H 2 O, stirring speed 150r / min, stirring for 4h to make it completely dissolved, slowly dropwise adding ammonia water to the solution to adjust the pH of the solution to 8.0, and obtain a solid precipitate after filtration, place it in a drying oven at 120°C for 6h, and then 10.02g of nano-cobalt aluminate was obtained after roasting at 1200°C for 3 hours in a Furnace;
[0033] (2) Add the obtained nano-cobalt aluminate, 85.86g of titanium dioxide (purity: 99wt%), and 11.18g of nitric acid solution (purity: 30wt%) into 107mL of deionized water in sequence, stirring at a speed of 300r / min, and stirring for 6h Mix well afterwards. The mixture is extruded in an extruder, dried in a drying oven at 120°C for 6 hours, and then roasted in a muffle furnace at 500°C for 6 hours to obtain a shaped carrier;
[0034] (3) 12.65g of Fe(NO 3 ) 3 9H 2 O was dissolved in deionized w...
Embodiment 2
[0037] (1) Add 20 mL of deionized water and 1.65 g of Co(NO 3 ) 2 ·6H 2 O and 2.12g of Al(NO 3 ) 3 9H 2 O, stirring speed 100r / min, stirring for 2h to make it completely dissolved, slowly dropwise adding ammonia water to the solution to adjust the pH of the solution to 10.0, and obtain a solid precipitate after filtration, place it in a drying oven at 80°C for 2h, and then 0.99g of nano-cobalt aluminate was obtained after calcination at 800°C for 2 hours in a Furnace;
[0038] (2) The obtained nano-cobalt aluminate and 98.99g of titanium dioxide (purity 99wt%), 11.67g of nitric acid solution (purity 30wt%) were added to 111.66mL of deionized water successively, stirring speed 200r / min, stirring Mix well after 4h. The mixture is extruded in an extruder, dried in a drying oven at 80°C for 2 hours, and then roasted in a muffle furnace at 200°C for 2 hours to obtain a shaped carrier;
[0039] (3) 2.53g of Fe(NO 3 ) 3 9H 2 O was dissolved in deionized water to make a 45mL...
Embodiment 3
[0042] (1) Add 350 mL of deionized water and 24.68 g of Co(NO 3 ) 2 ·6H 2 O and 31.81g of Al(NO 3 ) 3 9H 2 O, the stirring speed is 200r / min, stir for 4h to make it completely dissolved, slowly add ammonia water dropwise to the solution to adjust the pH of the solution to 6.0, obtain a solid precipitate after filtration, place it in a drying oven at 120°C for 8h, and then 15.06g of nano-cobalt aluminate was obtained after calcination at 1200°C for 4 hours in a Furnace;
[0043] (2) The obtained nano-cobalt aluminate and 75.76g of titanium dioxide (purity 99wt%), 10.59g of nitric acid solution (purity 30wt%) were added to 101.35mL of deionized water successively, stirring speed 400r / min, stirring Mix well after 8h. The mixture is extruded in an extruder, dried in a drying oven at 120°C for 8 hours, and then roasted in a muffle furnace at 400°C for 6 hours to obtain a shaped carrier;
[0044] (3) 25.30g of Fe(NO 3 ) 3 9H 2 O was dissolved in deionized water to prepare ...
PUM
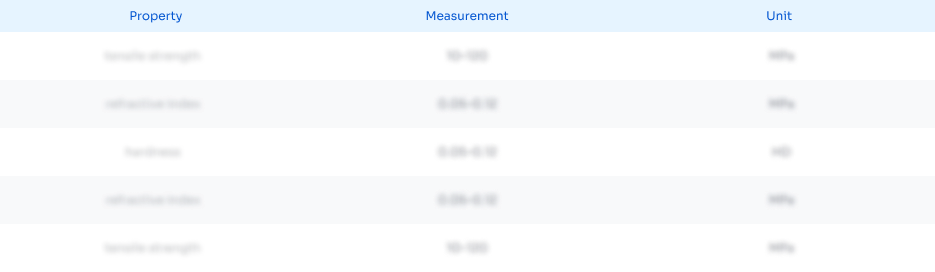
Abstract
Description
Claims
Application Information

- R&D
- Intellectual Property
- Life Sciences
- Materials
- Tech Scout
- Unparalleled Data Quality
- Higher Quality Content
- 60% Fewer Hallucinations
Browse by: Latest US Patents, China's latest patents, Technical Efficacy Thesaurus, Application Domain, Technology Topic, Popular Technical Reports.
© 2025 PatSnap. All rights reserved.Legal|Privacy policy|Modern Slavery Act Transparency Statement|Sitemap|About US| Contact US: help@patsnap.com