Base metal wire rod special for 1,420 MPa-level PC steel bar and preparation method of base metal wire rod
A wire rod and base metal technology, applied in the field of steel rolling, can solve the problems of delayed fracture, long heating time, residual stress of quenching cracking, etc.
- Summary
- Abstract
- Description
- Claims
- Application Information
AI Technical Summary
Problems solved by technology
Method used
Image
Examples
preparation example Construction
[0023] The preparation method of the base metal wire rod for 1420MPa grade PC steel bar of the present invention comprises heating, rough rolling and pre-finish rolling, pre-controlled cooling, finish rolling, controlled cooling, silk spinning and slow cooling process, specifically comprising the following steps:
[0024] A. Heating: Send the billet into the heating furnace and heat it to 1040-1070°C. The billet includes the following chemical components in terms of mass percentage: C: 0.27%-0.32%, Si: 0.80%-1.00%, Mn: 1.0% ~1.20%, Ti:0.010~0.017%, P≤0.025%, S≤0.025%, Mo≤0.010%, N:≤0.0060%; and Si+Mn≤2.0%, Si:N≥160; the rest are Fe and unavoidable impurities;
[0025] B. Rough intermediate rolling and pre-finishing rolling: the heated billet is rolled for 18 passes, the starting rolling temperature is 1040-1070°C, and the total rolling reduction is 98.0%-98.6%;
[0026] C. Pre-cooling: Cool the rolled piece after leaving the pre-finishing unit in two stages, and carry out bac...
Embodiment 1
[0037] A cold billet of 150mm×150mm is fed into a heating furnace for heating. The billet contains the following chemical components in mass percentage: C: 0.30%, Si: 0.80%, Mn: 1.18%, Ti: 0.010%, P: 0.013%, S:0.019%, Mo:0.008%, N:0.0045%, Si+Mn=21.98%, Si:N=177; the rest is Fe and unavoidable impurities; The time is 60 minutes, and the steel billet after being released from the furnace is subjected to 18 passes of finish rolling and pre-finish rolling, with a total reduction rate of 98.6%, and a rolling start temperature of 1040°C, to obtain a pre-finish rolling piece. The rolled piece after pre-finish rolling is cooled by water in 2 stages, with a total water volume of 216m 3 / h, the ratio of water is 1.0:1.0, back-purging is carried out after inter-stage water cooling, and a 940°C rolling stock is obtained. The 940°C finishing rolling piece is then subjected to 6 passes of finishing rolling by the finishing rolling unit, and the total reduction rate of finishing rolling is...
Embodiment 2
[0040] Send a 150mm×150mm cold billet into a heating furnace for heating. The chemical composition of the billet is calculated by mass percentage: C: 0.27%, Si: 0.99%, Mn: 1.01%, Ti: 0.015%, P: 0.016% , S:0.020%, Mo:0.005%, N:0.0060%, Si+Mn=2.0%, Si:N=165; the rest is Fe and unavoidable impurities. The steel billet stays in the soaking section for 35 minutes, and the total time in the furnace is 80 minutes. The steel billet after being released from the furnace is subjected to 18 passes of finish rolling and pre-finish rolling. Rolled pieces. The rolled piece after pre-finish rolling is cooled by water in 2 stages, with a total water volume of 216m 3 / h, the ratio of water is 1:1, back-purging is carried out after inter-stage water cooling, and a 970°C rolling stock is obtained. The 970°C finishing rolling piece is then subjected to 6 passes of finishing rolling by the finishing rolling unit, and the total reduction rate of finishing rolling is 70%. The rolled piece after f...
PUM
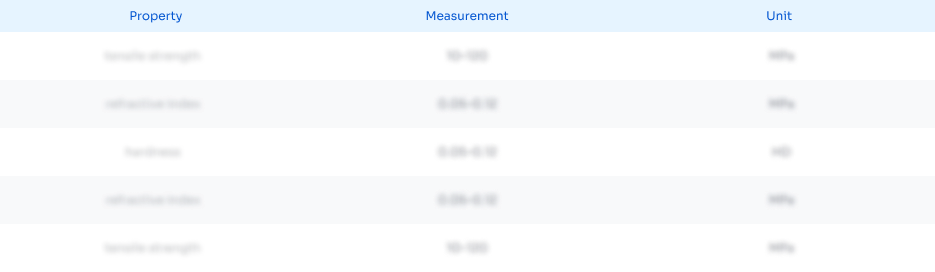
Abstract
Description
Claims
Application Information

- R&D
- Intellectual Property
- Life Sciences
- Materials
- Tech Scout
- Unparalleled Data Quality
- Higher Quality Content
- 60% Fewer Hallucinations
Browse by: Latest US Patents, China's latest patents, Technical Efficacy Thesaurus, Application Domain, Technology Topic, Popular Technical Reports.
© 2025 PatSnap. All rights reserved.Legal|Privacy policy|Modern Slavery Act Transparency Statement|Sitemap|About US| Contact US: help@patsnap.com