Dehydrogenation catalyst and application thereof in preparation of divinylbenzene by dehydrogenation of diethylbenzene
A dehydrogenation catalyst and catalyst technology, applied in the field of catalytic chemistry, can solve problems such as surface coking, low monodiene ratio, catalytic performance and production requirements, and product quality mismatches
- Summary
- Abstract
- Description
- Claims
- Application Information
AI Technical Summary
Problems solved by technology
Method used
Image
Examples
Embodiment 1
[0021] 40g of lanthanide-modified heteropolyacid K 13 [La(SiW 9 Mo 2 o 39 ) 2 ]·nH 2 O. 20g of macroporous cross-linked polymer with a particle size of 10–20nm supported nano-α-Fe 2 o 3 , 40g CeO 2 Stir in the kneader for 1.5 hours, add deionized water accounting for 24.6% of the catalyst raw material gross weight, stir for 0.5 hours, take out the extruded pellets, dry for 4 hours at 80 ° C, then place in a nitrogen atmosphere box furnace, Calcined at 300°C for 2 hours to obtain the finished catalyst.
[0022] 10mL of catalyst was loaded into the fixed-bed continuous flow reaction device to directly catalyze the selective dehydrogenation of diethylbenzene to prepare divinylbenzene. Nitrogen is used as the carrier gas, the preheater temperature is 200°C, the reaction temperature is 450°C, and the volumetric space velocity of diethylbenzene is 3h –1 , the reaction results are shown in Table 1.
[0023] Table 1
[0024]
Embodiment 2-5
[0026] Catalyst and reaction condition are the same as embodiment 1, only change temperature of reaction, and the reaction time is 1 day, and reaction result is as table 2.
[0027] Table 2
[0028]
Embodiment 6-8
[0030] Catalyst and reaction condition are the same as embodiment 1, only volume space velocity is changed, and reaction time is 1 day, and reaction result is shown in table 3.
[0031] table 3
[0032]
PUM
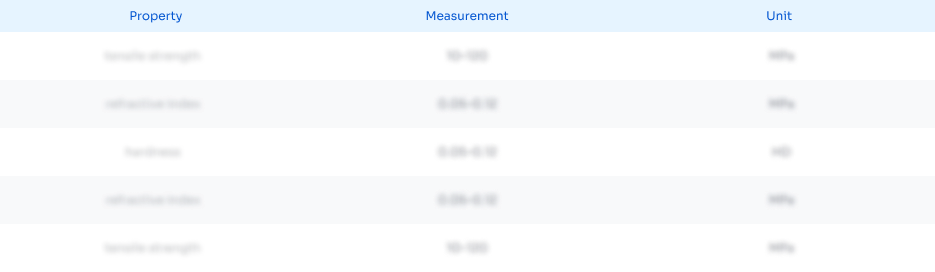
Abstract
Description
Claims
Application Information

- R&D Engineer
- R&D Manager
- IP Professional
- Industry Leading Data Capabilities
- Powerful AI technology
- Patent DNA Extraction
Browse by: Latest US Patents, China's latest patents, Technical Efficacy Thesaurus, Application Domain, Technology Topic, Popular Technical Reports.
© 2024 PatSnap. All rights reserved.Legal|Privacy policy|Modern Slavery Act Transparency Statement|Sitemap|About US| Contact US: help@patsnap.com