A method for removing grinding burrs on crankshaft journal edge and shoulder surface
A technology for crankshaft journals and shoulders is applied in the field of grinding burrs on the edges of crankshaft journals and shoulder surfaces, which can solve problems such as incomplete deburring, and achieve low cost, good effect and the effect of reducing grinding burrs.
- Summary
- Abstract
- Description
- Claims
- Application Information
AI Technical Summary
Problems solved by technology
Method used
Image
Examples
Embodiment
[0027] A method of removing the edge of the crankshaft neck and the shoulder grinding burr, the crankshaft processing is carried out according to the normal machining process.
[0028] The method includes the following steps:
[0029] 1) In the secondary rod of the main axis and the sinking tank, the cenon lathe is taken with the edge of the main shaft neck and shoulder and shoulder, and the chamfered direction is inclined with the shoulder grinding surface. The angular angle is 25 ° -30 °, the chamfer width is 0.07-0.15mm than the grinding margin, such as image 3 As shown, the chamfer speed is 900-1300r / min, the feed amount is 0.06-0.15mm / r, the roughness is Ra0.8-Ra1.0μm, the processing margin reserved for the shoulder is 0.12-0.30mm, shoulder The surface roughness is Ra1.0-Ra 1.6 μm;
[0030] 2) In the case of the main axial neck and the sinking tank process, the cenquetal neck sink is taken on the edge of the spindle neck, and the chamfer direction is inclined with the jo...
PUM
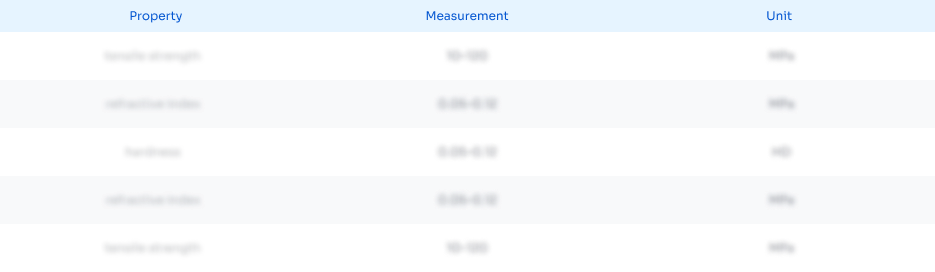
Abstract
Description
Claims
Application Information

- R&D Engineer
- R&D Manager
- IP Professional
- Industry Leading Data Capabilities
- Powerful AI technology
- Patent DNA Extraction
Browse by: Latest US Patents, China's latest patents, Technical Efficacy Thesaurus, Application Domain, Technology Topic, Popular Technical Reports.
© 2024 PatSnap. All rights reserved.Legal|Privacy policy|Modern Slavery Act Transparency Statement|Sitemap|About US| Contact US: help@patsnap.com