Anti-pilling flannel production process and production device
A ball flannel, technology for producing devices, applied in textile and papermaking, fabric surface trimming, fabric elongation, etc.
- Summary
- Abstract
- Description
- Claims
- Application Information
AI Technical Summary
Problems solved by technology
Method used
Image
Examples
specific Embodiment approach 1
[0036] Such as Figure 1 to Figure 14 As shown, an anti-pilling flannel and production device includes a processing frame 1, a combined drive 2, two stretching regulators 3, a plurality of stretching rotating cylinders 4, an upper intermittent fixing seat 5 and a lower intermittent fixing seat 6, the combined driver 2 is rotatably connected in the processing frame 1, the two stretch regulators 3 are fixedly connected to the combined driver 2, and a plurality of stretch rotating cylinders 4 are evenly fixedly connected to the two stretch regulators. Between the devices 3, the lower end of the upper intermittent fixing seat 5 and the upper end of the lower intermittent fixing seat 6 are all slidably connected to the combined drive 2, and the upper intermittent fixing seat 5 and the lower intermittent fixing seat 6 are all longitudinally slidably connected in the processing frame 1 . The flannel that has just been dried and produced first passes between the processing frame 1 an...
specific Embodiment approach 2
[0038] Such as Figure 1 to Figure 14 As shown, this embodiment will further explain Embodiment 1. The processing frame 1 includes a bottom plate 1-1, a motor fixing seat 1-2, a rotating shaft rotating seat 1-3, two longitudinal fixing plates 1-4, an upper Clamping and fixing stainless steel roller 1-5, lower clamping and fixing stainless steel roller 1-6 and multiple longitudinal chute 1-7, motor fixing seat 1-2 and rotating shaft rotating seat 1-3 are respectively fixedly connected to the base plate 1-1 At the front and rear ends, the two longitudinal fixing plates 1-4 are fixedly connected to the bottom plate 1-1, and the upper clamping and fixing stainless steel roller 1-5 and the lower clamping and fixing stainless steel roller 1-6 are fixedly connected to the two longitudinal fixing plates Between 1-4, the two longitudinal fixing plates 1-4 are provided with a plurality of longitudinal slide grooves 1-7 that run through from front to back. The flannel that has just been...
specific Embodiment approach 3
[0040] Such as Figure 1 to Figure 14 As shown, this embodiment will further illustrate the second embodiment. The combined driver 2 includes a drive motor 2-1, a tension drive shaft 2-2, a main drive pulley 2-3, a slave drive pulley 2-4, an intermittent Fix the driving shaft 2-5 and two driving double-convex driving wheels 2-6, the driving motor 2-1 is fixedly connected on the motor fixing seat 1-2, and one end of the stretching driving shaft 2-2 is connected to the driving motor through a coupling 2-1 of the drive shaft, the other end of the stretching drive shaft 2-2 is connected to the rotating shaft revolving seat 1-3, the main drive pulley 2-3 is fixedly connected to the drive shaft of the drive motor 2-1, the main drive pulley 2-3 is connected to the slave drive pulley 2-4 through a belt drive, and the slave drive pulley 2-4 is fixedly connected to the intermittently fixed drive shaft 2-5, and the intermittently fixed drive shaft 2-5 is rotatably connected to two longit...
PUM
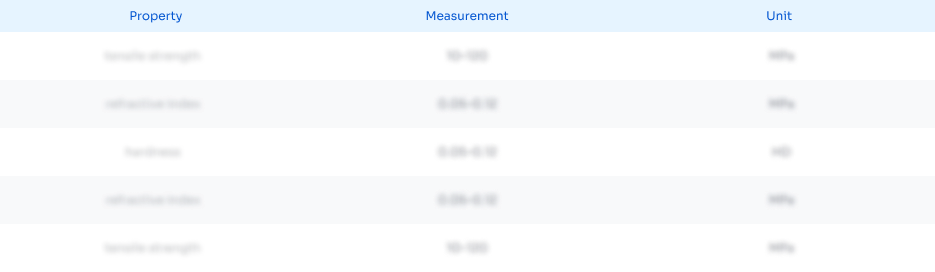
Abstract
Description
Claims
Application Information

- Generate Ideas
- Intellectual Property
- Life Sciences
- Materials
- Tech Scout
- Unparalleled Data Quality
- Higher Quality Content
- 60% Fewer Hallucinations
Browse by: Latest US Patents, China's latest patents, Technical Efficacy Thesaurus, Application Domain, Technology Topic, Popular Technical Reports.
© 2025 PatSnap. All rights reserved.Legal|Privacy policy|Modern Slavery Act Transparency Statement|Sitemap|About US| Contact US: help@patsnap.com