Mechanical and chemical activation coupled refractory iron ore pelletizing energy conservation and emission reduction method
An energy saving and emission reduction, iron ore technology, applied in the field of refractory iron ore pretreatment, can solve problems such as poor roasting performance of refractory iron ore, and achieve the advantages of reducing energy consumption of pellets, increasing specific surface area and activity, and reducing energy consumption. Effect
- Summary
- Abstract
- Description
- Claims
- Application Information
AI Technical Summary
Problems solved by technology
Method used
Image
Examples
Embodiment 1
[0031] For the specularite in Table 1, adding 1.0% CaO content to the specularite is 54.2% limestone, the content of limestone less than 0.045mm is 80%, the content less than 0.02mm is 33%, and the moisture of limestone is controlled at 7.5%, after the limestone is added to the specularite, it is mixed with a horizontal strong mixer with coulter-type stirring blades, the stirring speed is 4r / min, and then high-pressure roller milling under the conditions of 2.5MPa and 7.5% moisture, The grate-rotary kiln is used for roasting, the temperature rise rate of the grate preheating stage I is controlled to be 100°C / min, and the decomposition ratio of limestone before entering the roasting reaches 90%. Compared with the conventional pellet preparation and sintering process of Example 1, the optimal pellet calcination temperature can be reduced to 1260°C, the pellet strength can be increased to 2678N / piece, the energy consumption can be reduced by 19%, and the SO 2 22% reduction in emi...
Embodiment 2
[0033]For the specularite in Table 1, adding 1.5% CaO content to the specularite is 54.2% limestone, the content of limestone less than 0.045mm is 80%, the content less than 0.02mm is 33%, and the moisture of limestone is controlled at 7.0%, after the limestone is added to the specular iron ore, it is mixed with a horizontal strong mixer with a plow-type stirring blade, and the stirring speed is 6r / min, and then high-pressure roller milling under the conditions of 3.2MPa and 7.0% moisture, The grate-rotary kiln is used for roasting, the temperature rise rate of the grate preheating stage I is controlled to be 70°C / min, and the decomposition ratio of limestone before entering the roasting reaches 93%. Compared with the conventional pellet preparation and sintering process of Example 1, the optimal pellet calcination temperature can be reduced to 1240°C, the pellet strength can be increased to 2712N / piece, the energy consumption can be reduced by 25%, and the SO 2 30% reduction ...
Embodiment 3
[0035] For the hematite in Table 1, add 0.5% CaO to the hematite and add limestone with a content of 54.2%. The content of limestone less than 0.045mm is 80%, and the content less than 0.02mm is 33%. The moisture content of limestone is controlled at 7.0%, after limestone is added to hematite, it is mixed with a horizontal strong mixer with coulter-type stirring blades, and the stirring speed is 5r / min, and then high-pressure roller milling under the conditions of 2.5MPa and 6.5% moisture, The grate-rotary kiln is used for roasting, the temperature rise rate of the grate preheating stage I is controlled to be 85°C / min, and the decomposition ratio of limestone before entering the roasting reaches 92%. Compared with the conventional pellet preparation and sintering process in Example 1, the optimal pellet calcination temperature can be reduced from 1320°C to 1260°C, the strength of pellets can be increased from 2521N / piece to 2895N / piece, and the energy consumption can be reduced...
PUM
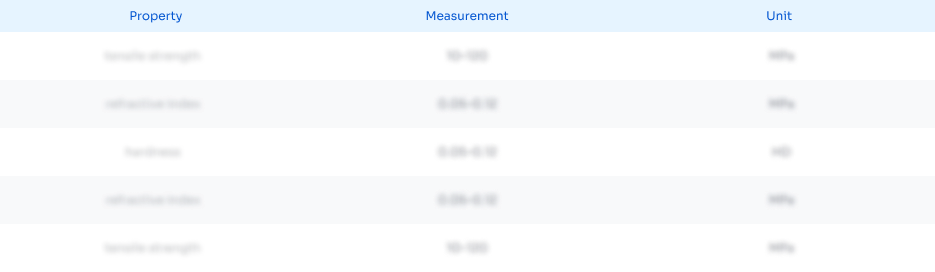
Abstract
Description
Claims
Application Information

- R&D Engineer
- R&D Manager
- IP Professional
- Industry Leading Data Capabilities
- Powerful AI technology
- Patent DNA Extraction
Browse by: Latest US Patents, China's latest patents, Technical Efficacy Thesaurus, Application Domain, Technology Topic, Popular Technical Reports.
© 2024 PatSnap. All rights reserved.Legal|Privacy policy|Modern Slavery Act Transparency Statement|Sitemap|About US| Contact US: help@patsnap.com