Full-automatic shell welding production line
A welding production line, fully automatic technology, applied in welding equipment, welding equipment, auxiliary welding equipment, etc., can solve the problem of the compressor shell prone to shaking position, offset and other problems, and achieve the effect of easy brushing operation.
- Summary
- Abstract
- Description
- Claims
- Application Information
AI Technical Summary
Problems solved by technology
Method used
Image
Examples
Embodiment 1
[0038] A fully automatic shell welding production line, such as Figure 1-3 As shown, it includes a conveyor line body 1, foot plate welding equipment 2, convex nail welding equipment 3 and position detection equipment 4 connected in sequence from left to right. The position detection device 4 is provided with a brushing mechanism 5, and the transmission line body 1 adopt 08B-U2 stainless steel chain and standard aluminum alloy profiles, and the upper and lower chains are in the form of pallets, the brushing mechanism 5 includes a brushing bottom plate 51, a brushing side plate 52 and a brushing motor 53, two brushing side plates 52 They are respectively fixedly mounted on the front and rear ends of the brushing base plate 51, and the upper end surfaces of the two brushing base plates 51 are fixedly installed with two brushing motors 53 with two stations, and the output of each brushing motor 53 Each end is provided with a brushing shaft 54, and the upper surface of the brushi...
Embodiment 2
[0043] Embodiment 2 is a further improvement on the basis of Embodiment 1, mainly for the purpose of simplifying the structure and having a better clamping and fixing effect, which will be described in detail below.
[0044] A fully automatic shell welding production line, such as figure 1 with Figure 5 As shown, it includes foot plate welding equipment 2, convex nail welding equipment 3 and position detection equipment 4 connected in sequence from left to right by the transmission line body 1. The position detection equipment 4 is equipped with a brushing mechanism 5, and the transmission line body 1 adopts 08B -U2 stainless steel chain and standard aluminum alloy profiles, and the upper and lower chains are in the form of pallets. The brushing mechanism 5 includes a brushing bottom plate 51, a brushing side plate 52 and a brushing motor 53. The two brushing side plates 52 are respectively Fixedly installed on the front and rear ends of the brushing base plate 51, the upper...
PUM
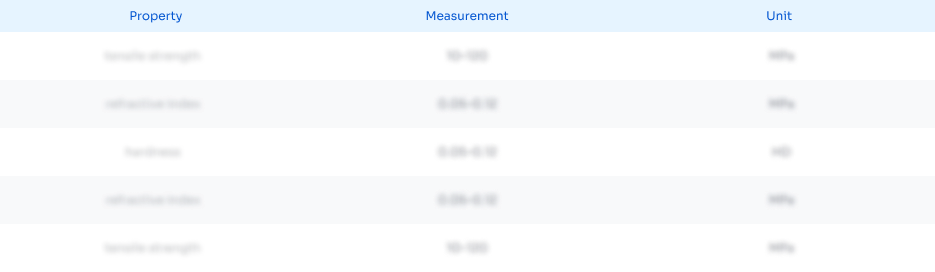
Abstract
Description
Claims
Application Information

- R&D
- Intellectual Property
- Life Sciences
- Materials
- Tech Scout
- Unparalleled Data Quality
- Higher Quality Content
- 60% Fewer Hallucinations
Browse by: Latest US Patents, China's latest patents, Technical Efficacy Thesaurus, Application Domain, Technology Topic, Popular Technical Reports.
© 2025 PatSnap. All rights reserved.Legal|Privacy policy|Modern Slavery Act Transparency Statement|Sitemap|About US| Contact US: help@patsnap.com