A coking coal blending method for increasing the average particle size of coke and improving the particle size distribution of coke
A technology of average particle size and particle size distribution, which is applied in the field of metallurgy, can solve the problems of coal blending in the coking coal market, increasing the difficulty of using coking coal, coal quality control and coke quality adjustment, etc., to achieve low professional requirements and optimize particle size The effect of easy distribution and operation
- Summary
- Abstract
- Description
- Claims
- Application Information
AI Technical Summary
Problems solved by technology
Method used
Image
Examples
Embodiment 1
[0044] 1. Determination of coke quality indicators for each coking single coal used in production, coking coal inertness capacity index (including: total expansion degree, inertness volume, inertness rate, maximum inertness capacity), coal micro-inertity group Coal content index, initial softening temperature, solidification temperature, single coal coke quality index (including: strength after reaction, coke particle size), according to the measurement results of single coal-coke quality index, carry out the following coal blending plan formulation steps:
[0045] (1) Coal microscopically inert component content 01 ≤8% Y 1 1 type of briquette, with a mass ratio of 15%;
[0046] (2) Coal microscopic inert component content 8% 2 ≤15% Y 2 One type of briquette, with a mass ratio of 20%;
[0047] (3) The content of coal microscopically inert components is 15%3 ≤35%, Y 3 2 kinds of briquettes (Y 3-1 , Y 3-2 ), the mass ratio is 45% (in which Y 3-1 15%, Y 3-2 20%);
[0048]...
Embodiment 2
[0053] 1. Determination of coke quality indicators for each coking single coal used in production, coking coal inertness capacity index (including: total expansion degree, inertness volume, inertness rate, maximum inertness capacity), coal micro-inertity group Coal content index, initial softening temperature, solidification temperature, single coal coke quality index (including: strength after reaction, coke particle size), according to the measurement results of single coal-coke quality index, carry out the following coal blending plan formulation steps:
[0054] (1) Coal microscopically inert component content 01 ≤8% Y 1 One type of briquette, with a mass ratio of 25%;
[0055] (2) Coal microscopic inert component content 8%2 ≤15% Y 2 1 type of briquette, with a mass ratio of 15%;
[0056] (3) The content of coal microscopically inert components is 15%3 ≤35%, Y 3 2 kinds of briquettes (Y 3-1 , Y 3-2 ), the mass ratio is 25% (where Y 3-1 15%, Y 3-2 20%);
[0057] (4)...
Embodiment 3
[0064] 1. Measure the coke quality index of each coking single coal used in production, draw a single coal-coke quality index comparison table, and determine the coal blending plan as follows:
[0065] (1) Coal microscopically inert component content 01 ≤8% Y 1 One type of briquette, with a mass ratio of 20%;
[0066] (2) Coal microscopic inert component content 8% 2 ≤15% Y 2 One type of briquette, with a mass ratio of 20%;
[0067] (3) The content of coal microscopically inert components is 15%3 ≤35%, Y 3 2 kinds of briquettes (Y 3-1 , Y 3-2 ), the mass ratio is 30% (where Y 3-1 15%, Y 3-2 20%);
[0068] (4) Coal microscopically inert component content 35% 4 ≤45% Y 4 One type of briquette, with a mass ratio of 20%;
[0069] (5) Select coal micro-inert component content 45%5 ≤60% of Y 5 1 type of briquette, with a mass ratio of 10%;
[0070] 2. Sampling according to the coal type and proportion determined in step 1, mixing and pulverizing, and measuring the coal mic...
PUM
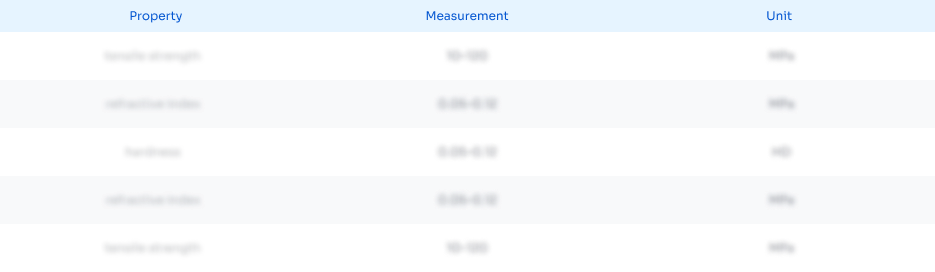
Abstract
Description
Claims
Application Information

- R&D Engineer
- R&D Manager
- IP Professional
- Industry Leading Data Capabilities
- Powerful AI technology
- Patent DNA Extraction
Browse by: Latest US Patents, China's latest patents, Technical Efficacy Thesaurus, Application Domain, Technology Topic, Popular Technical Reports.
© 2024 PatSnap. All rights reserved.Legal|Privacy policy|Modern Slavery Act Transparency Statement|Sitemap|About US| Contact US: help@patsnap.com