Vacuum perfusion epoxy resin system and preparation method and application thereof
An epoxy resin, vacuum infusion technology, applied in the direction of final product manufacturing, sustainable manufacturing/processing, wind power generation, etc., can solve the problems of short operation time, fast curing speed of epoxy resin, defects of composite materials, etc., and achieve low price , The effect of high mechanical strength and low reactivity of the product
- Summary
- Abstract
- Description
- Claims
- Application Information
AI Technical Summary
Problems solved by technology
Method used
Image
Examples
Embodiment 1
[0040] A kind of vacuum infusion epoxy resin system for wind power blades, it comprises A component and B component, and described A component comprises by weight percentage: Bisphenol A type epoxy resin 70%; Epoxy diluent I (multiple Epoxy tar) 30%, epoxy thinner II0%,;
[0041] The B component includes by weight percentage: polyetheramine curing agent 50%, isophorone diamine 50%;
[0042] The components A and B are mixed in a ratio of 100:25 by weight.
[0043] Wherein, the preparation method of the system is:
[0044] Step 1, prepare component A:
[0045] Put bisphenol A epoxy resin, epoxy diluent I and epoxy diluent II into the reactor; heat the reactor to 60°C and stir at 100rpm for 30 minutes, then stop; stop heating, cool to room temperature to get the obtained product The A component;
[0046] Step 2, prepare component B:
[0047] Add polyetheramine curing agent and isophorone diamine into the reaction kettle, stir at 100rpm for 30 minutes and then stop to obtain ...
Embodiment 2~7 and comparative example 1
[0050] The preparation methods of Examples 2-7 and Comparative Example 1 are the same as those of Example 1, and will not be repeated here. The difference lies in the proportioning composition. The proportioning composition of the vacuum infusion epoxy resin system of each embodiment sees the following table:
[0051]
[0052]
PUM
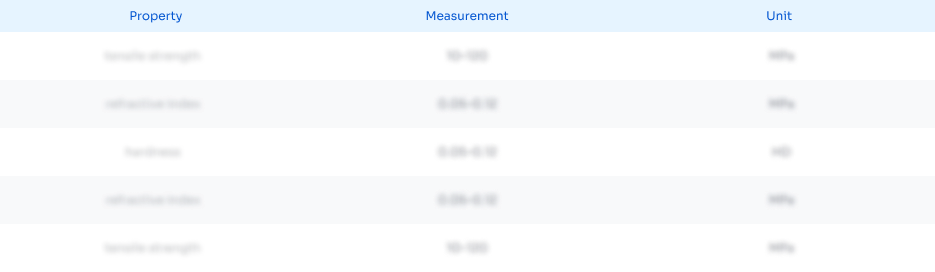
Abstract
Description
Claims
Application Information

- R&D
- Intellectual Property
- Life Sciences
- Materials
- Tech Scout
- Unparalleled Data Quality
- Higher Quality Content
- 60% Fewer Hallucinations
Browse by: Latest US Patents, China's latest patents, Technical Efficacy Thesaurus, Application Domain, Technology Topic, Popular Technical Reports.
© 2025 PatSnap. All rights reserved.Legal|Privacy policy|Modern Slavery Act Transparency Statement|Sitemap|About US| Contact US: help@patsnap.com