Multi-component water-resistant catalyst for preparing carboxylic ester through aldehyde oxidative esterification, preparation and manufacturing of carboxylic ester
A technology of aldehyde oxidation esterification and oxidative esterification, which is applied in the field of new multi-component water-resistant catalysts, can solve the problems of unsatisfactory market demand and technology monopoly, and achieve high mechanical strength and chemical stability, low cost and simple preparation method Effect
- Summary
- Abstract
- Description
- Claims
- Application Information
AI Technical Summary
Problems solved by technology
Method used
Image
Examples
Embodiment 1
[0038]Mix 10g of 30% silica sol (pH=4.5), 3.0g of aluminum nitrate nonahydrate, 1.96g of magnesium hydroxide, 3g of concentrated nitric acid with a concentration of 65%, and 60mL of deionized water at 25°C, and keep the mixture at 50°C for stirring and aging After 24 hours, a homogeneous solid solution suspension was obtained, and the water was removed by rotary evaporation, and vacuum-dried at 80° C. to obtain a white powdery solid. The solid was placed in a tube furnace and roasted under a nitrogen gas temperature program. Starting at 30°C, the temperature was raised to 300°C at a rate of 2.25°C / min, kept at 300°C for 4 hours, and then started at 300°C, and the temperature was raised at a rate of 2.5°C / min. To 600°C, keep at 600°C for 4h. After natural cooling, the Si-Mg-Al metal composite oxide carrier is obtained, in which the magnesium oxide, silicon oxide, and aluminum oxide in the composite oxide carrier combine to form a solid solution, which improves the acid and alka...
Embodiment 2
[0040] Mix 10g of 30% silica sol (pH=4.5), 1.8757g of aluminum nitrate nonahydrate, 0.2916g of magnesium hydroxide, 1.7812g of zirconium oxychloride, 2g of concentrated nitric acid with a concentration of 80%, and 60mL of deionized water at 25°C. The mixture was kept at 50° C. for 24 h with stirring to obtain a uniform solid solution suspension, which was evaporated to remove water, and dried in vacuum at 80° C. to obtain a white powdery solid. Put the solid in a tube furnace, and roast it under nitrogen with programmed temperature rise, heating at 30-300°C for 3 hours (heating rate 1.5°C / min), keeping at 300°C for 4 hours, heating at 300-600°C for 3 hours (heating rate 1.7°C / min) , keep at 600°C for 4h. After natural cooling, the Si-Mg-Al-Zr metal composite oxide carrier is obtained.
Embodiment 3
[0042] Mix 10g of 30% silica sol (pH=4.5), 1.8757g of aluminum nitrate nonahydrate, 4.33g of lanthanum nitrate hexahydrate, 3g of concentrated nitric acid with a mass concentration of 60%, and 100mL of deionized water, and keep the mixture at 50°C for 24h with stirring to obtain a uniform The solid solution suspension was evaporated to remove water, and dried under vacuum at 80°C to obtain a white powdery solid. Put the solid in a tube furnace, and roast it under nitrogen with programmed temperature rise, heating at 30-300°C for 3 hours (heating rate 1.5°C / min), keeping at 300°C for 4 hours, heating at 300-600°C for 3 hours (heating rate 1.7°C / min) , keep at 600°C for 4h. After natural cooling, the Si-La-Al metal composite oxide carrier is obtained.
PUM
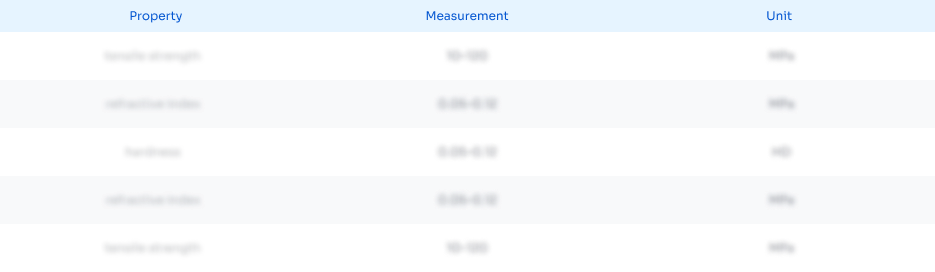
Abstract
Description
Claims
Application Information

- R&D Engineer
- R&D Manager
- IP Professional
- Industry Leading Data Capabilities
- Powerful AI technology
- Patent DNA Extraction
Browse by: Latest US Patents, China's latest patents, Technical Efficacy Thesaurus, Application Domain, Technology Topic, Popular Technical Reports.
© 2024 PatSnap. All rights reserved.Legal|Privacy policy|Modern Slavery Act Transparency Statement|Sitemap|About US| Contact US: help@patsnap.com