Resin-based carbon fiber composite permanent magnet conductive contact and manufacturing method thereof
A conductive contact and manufacturing method technology, applied in the direction of contacts, circuits, electric switches, etc., can solve the problems of poor stability of conductive network, low linearity, obvious hysteresis of sensors, etc., and achieve good fit, long service life, The effect of low energy consumption
- Summary
- Abstract
- Description
- Claims
- Application Information
AI Technical Summary
Problems solved by technology
Method used
Examples
Embodiment 1
[0026] A resin-based carbon fiber composite permanent magnet conductive contact, the composite permanent magnet conductive contact is composed of two parts: a core and a coil, wherein the core is a cylindrical NdFeB permanent magnet core, and the conductor is an aniline modified carbon fiber aluminum core Composite wire, epoxy resin, sub-medium temperature epoxy resin curing agent, starch grafted sodium acrylate mechanically blended secondary vulcanization glue is the composite core of the package curing material; the coil is made of aniline modified carbon fiber aluminum wound on the surface of the core Composition of epoxy resin for core composite wire and curing coil, secondary medium temperature epoxy resin curing agent, starch grafted sodium acrylate mechanically blended primary vulcanizate;
[0027] The manufacturing method of the above-mentioned conductive contact comprises the following steps:
[0028] 1) Raw material preparation
[0029] ① Raw material preparation: P...
Embodiment 2
[0045] The whole is consistent with Example 1, the difference is:
[0046] ① Raw material preparation: Prepare 250g of cylindrical NdFeB magnetic core, sufficient amount of thionyl chloride, sufficient amount of phenylenediamine, 1000g of epoxy resin, 150g of sub-medium temperature epoxy resin curing agent, and 10g of starch grafted sodium acrylate by weight , vulcanizing agent 8g, silane coupling agent 10g, graphite powder 50g, sufficient carbon fiber aluminum core composite wire, ammonium persulfate initiator 2g;
Embodiment 3
[0048] The whole is consistent with Example 1, the difference is:
[0049] ① Raw material preparation: Prepare 200g of cylindrical NdFeB magnetic core, sufficient amount of thionyl chloride, sufficient amount of phenylenediamine, 1000g of epoxy resin, 200g of sub-medium temperature epoxy resin curing agent, and 15g of starch grafted sodium acrylate by weight , Vulcanizing agent 10g, silane coupling agent 15g, graphite powder 80g, sufficient carbon fiber aluminum core composite wire, ammonium persulfate initiator 5g;
PUM
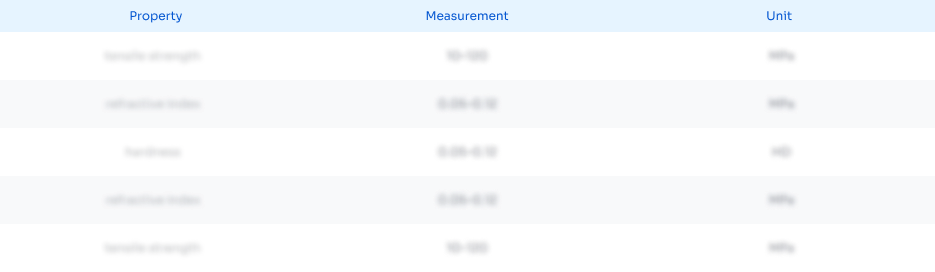
Abstract
Description
Claims
Application Information

- R&D Engineer
- R&D Manager
- IP Professional
- Industry Leading Data Capabilities
- Powerful AI technology
- Patent DNA Extraction
Browse by: Latest US Patents, China's latest patents, Technical Efficacy Thesaurus, Application Domain, Technology Topic, Popular Technical Reports.
© 2024 PatSnap. All rights reserved.Legal|Privacy policy|Modern Slavery Act Transparency Statement|Sitemap|About US| Contact US: help@patsnap.com