Continuous ore grinding reverse-direct flotation method for siliceous-calcareous collophanite
A collophosphate and siliceous phosphate technology, which is applied in the field of continuous grinding and reverse flotation of siliceous colloidal phosphate rock, can solve the problems of muddy running, high consumption of new water, deterioration of mineral processing indicators, etc., and achieve stable technological process, Low cost of treatment and the effect of reducing the dose of medicine
- Summary
- Abstract
- Description
- Claims
- Application Information
AI Technical Summary
Problems solved by technology
Method used
Image
Examples
Embodiment 1
[0026] Example 1, a method of continuous grinding and reverse flotation of siliceous calcareous collophosphine: after the crushed raw ore is subjected to two stages of continuous grinding and grading operations, it is firstly demagnesified by reverse flotation and then desiliconized by positive flotation The flotation process; the reverse flotation backwater enters the reverse flotation backwater tank and then returns to the reverse flotation for magnesium removal, the positive flotation backwater enters the positive flotation backwater tank and then returns to the positive flotation desiliconization operation, and the surplus positive flotation The return water is fed into the reverse flotation return tank for reverse flotation.
[0027] Two-stage continuous grinding until the grinding fineness is -200 mesh accounts for 95%. Reverse flotation demagnesia and forward flotation desiliconization are carried out according to the conventional process.
Embodiment 2
[0028] Embodiment 2, a kind of continuous grinding ore reverse flotation method of siliceous calcareous colloidal phosphate rock, its steps are as follows:
[0029] (1) After the crushed raw ore is fed into the two-stage continuous grinding and grading operation, the ground pulp is fed into the reverse flotation magnesium removal operation, and the products in the flotation machine tank are fed into the reverse flotation coarse concentrate dehydration operation, and the filtrate is It is fed into the reverse flotation backwater pool, the foam product is sent into the tailings pond or tailings stockpile after dehydration, and the filtrate is fed into the reverse flotation backwater pool; the products in the flotation machine tank are fed into the reverse flotation coarse concentrate dehydration operation, The filtrate is fed into the reverse flotation return pool, the foam product is sent to the tailings pond or tailings stockyard after dehydration, and the filtrate is fed into ...
Embodiment 3
[0038] Example 3, a method of continuous grinding and reverse flotation of silicon-calcium collophosphine: after the crushed raw ore is subjected to two-stage continuous grinding and classification operations, it is firstly demagnesified by reverse flotation, and then desiliconized by positive flotation The flotation process; the reverse flotation backwater enters the reverse flotation backwater tank and then returns to the reverse flotation for magnesium removal, the positive flotation backwater enters the positive flotation backwater tank and then returns to the positive flotation desiliconization operation, and the surplus positive flotation The return water is fed into the reverse flotation return tank for reverse flotation.
[0039] The two-stage continuous grinding method is as follows: the crushed phosphate rock is first fed into a stage of grinding operation, and after grinding, it is fed into a stage of classification operation, the grinding fineness is -200 mesh and 7...
PUM
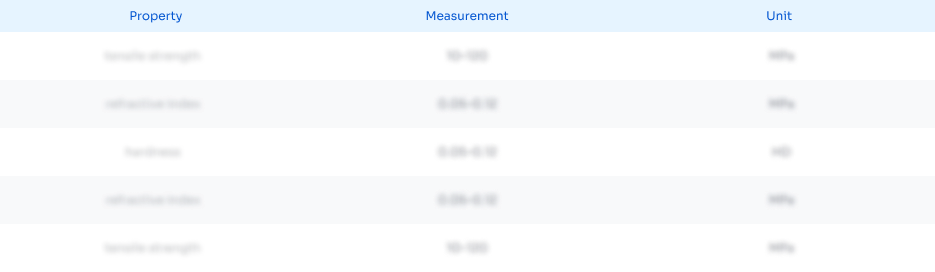
Abstract
Description
Claims
Application Information

- Generate Ideas
- Intellectual Property
- Life Sciences
- Materials
- Tech Scout
- Unparalleled Data Quality
- Higher Quality Content
- 60% Fewer Hallucinations
Browse by: Latest US Patents, China's latest patents, Technical Efficacy Thesaurus, Application Domain, Technology Topic, Popular Technical Reports.
© 2025 PatSnap. All rights reserved.Legal|Privacy policy|Modern Slavery Act Transparency Statement|Sitemap|About US| Contact US: help@patsnap.com