Polishing device used for sheet metal machining
A sheet metal and grinding plate technology, which is applied in the direction of grinding drive devices, metal processing equipment, grinding/polishing safety devices, etc., can solve problems such as poor adjustability, low grinding flexibility, and strict requirements for fixing parts, and achieve improved Improve the quality of machining, improve the quality of grinding, and improve the flexibility of grinding
- Summary
- Abstract
- Description
- Claims
- Application Information
AI Technical Summary
Problems solved by technology
Method used
Image
Examples
Embodiment 1
[0025] Such as Figure 1-4 As shown, a grinding device for sheet metal processing includes a mounting base 1, on which a column 2 is symmetrically fixed, and a cross bar 3 is arranged between the column 2, and a cross bar 3 is movably installed with The first motor 4, the output shaft 5 of the first motor 4 is provided with a grinding plate 6, the lower side of the grinding plate 6 is evenly provided with a grinding brush 7, and the lower side of the grinding plate 6 is provided with a mounting plate 19 , the mounting plate 19 is rotatably connected with a roller 18, the motor is provided with a slider 8, the cross bar 3 is provided with a chute 11, the slider 8 cooperates with the chute 11, and the chute 11 A worm 9 is fixedly connected to the block 8, and the worm 9 is installed in a chute 11, and the worm 9 is connected with a turbine 10, and the turbine 10 is connected with a power unit.
[0026] Specifically, the first motor 4 is installed on the crossbar 3, and the grin...
Embodiment 2
[0037] This embodiment is a further improvement and limitation of embodiment 1 on the basis of embodiment 1.
[0038] A kind of grinding device for sheet metal processing, including all parts in embodiment 1, also includes:
[0039] Further, the lower side of the drum 18 is provided with a water tank 21 filled with polishing fluid 211, the water tank 21 is provided with a filter screen 210, and the bottom of the water tank 21 is equipped with a water pump 22, and the water pump 22 is connected to the water pipe 12 , the crossbar 3 is equipped with a nozzle 13, the nozzle 13 is aligned with the grinding plate 6, the nozzle 13 is fixedly connected to the crossbar 3 through a water pipe 12, and a hose 15 is connected between the water pipe 12 and the column 2, The water pipe 12 is connected to a hose 15 through a connector 14 .
[0040] Specifically, in the process of parts grinding, due to the difference of parts materials, the same grinding brush 7 may have completely differen...
PUM
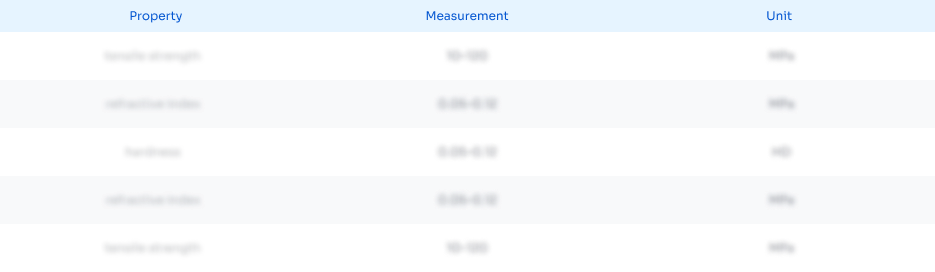
Abstract
Description
Claims
Application Information

- Generate Ideas
- Intellectual Property
- Life Sciences
- Materials
- Tech Scout
- Unparalleled Data Quality
- Higher Quality Content
- 60% Fewer Hallucinations
Browse by: Latest US Patents, China's latest patents, Technical Efficacy Thesaurus, Application Domain, Technology Topic, Popular Technical Reports.
© 2025 PatSnap. All rights reserved.Legal|Privacy policy|Modern Slavery Act Transparency Statement|Sitemap|About US| Contact US: help@patsnap.com