A kind of zrc/sic/c composite phase ceramic precursor material and preparation method thereof
A technology of multiphase ceramics and precursors, which is applied in the field of ZrC/SiC/C multiphase ceramic precursors and their preparation, can solve the problems of limited reaction activity of zirconocene dichloride, limited amount of zirconium introduced, and long time consumption.
- Summary
- Abstract
- Description
- Claims
- Application Information
AI Technical Summary
Problems solved by technology
Method used
Image
Examples
Embodiment 1
[0043] In this example, the ZrC / SiC / C composite ceramic precursor was prepared by the following method:
[0044] (1) A 100mL dry three-necked bottle, equipped with a rubber stopper, a condenser tube, and a three-way joint, put in a stirring magnet, added 1.46g (5.0mmol) zirconocene dichloride, 0.41g (5.0mmol) polydimethyl For silicon acetylene, vacuumize and fill the system with argon several times to replace the air in the system, then add 10mL of tetrahydrofuran and mix well;
[0045] (2) Cool the reaction flask containing the mixture of step (1) to -60°C, add 4.2mL (10.0mmol) 2.4M n-hexane solution of n-butyllithium dropwise to the reaction flask under stirring, and control the temperature of the system at - 40°C, after the dropwise addition, remove the cooling bath;
[0046] (3) The system in which n-butyllithium was added dropwise in step (2) was raised to 20° C. and continued to stir and react for 24 hours, and a white solid salt was precipitated in the system;
[0047...
Embodiment 2
[0050] In this example, the ZrC / SiC / C composite ceramic precursor was prepared by the following method:
[0051] (1) A 100mL dry three-necked bottle, equipped with a rubber stopper, a condenser tube, and a three-way joint, put it into a stirring magnet, and added 1.46g (5.0mmol) of zirconocene dichloride, 0.82g (10.0mmol) of polydimethyl For silicon acetylene, vacuumize and fill the system with argon several times to replace the air in the system, then add 12mL of tetrahydrofuran and mix well;
[0052] (2) Cool the reaction flask containing the mixture of step (1) to -60°C, add 4.2mL (10.0mmol) 2.4M n-hexane solution of n-butyllithium dropwise to the reaction flask under stirring, and control the temperature of the system at - 40°C, after the dropwise addition, remove the cooling bath;
[0053] (3) The system in which n-butyllithium was added dropwise in step (2) was raised to 20° C. and continued to stir and react for 24 hours, and a white solid salt was precipitated in the ...
Embodiment 3
[0057] This example is based on Example 1. In step (1), the added amount of polydimethylsilylacetylene is adjusted to 0.492g (6.0mmol), the added amount of tetrahydrofuran is 10.4mL, and the rest of the implementation methods are the same as the examples 1. The precursor was cured at 250 °C for 2 h in an argon atmosphere, and then pyrolyzed at 1600 °C for 2 h in an argon atmosphere to obtain a black ceramic product. XRD and elemental analysis showed that the product was a ZrC / SiC / C composite ceramic with a Zr content of 57.5 wt%, Si content is 15.3 wt%.
PUM
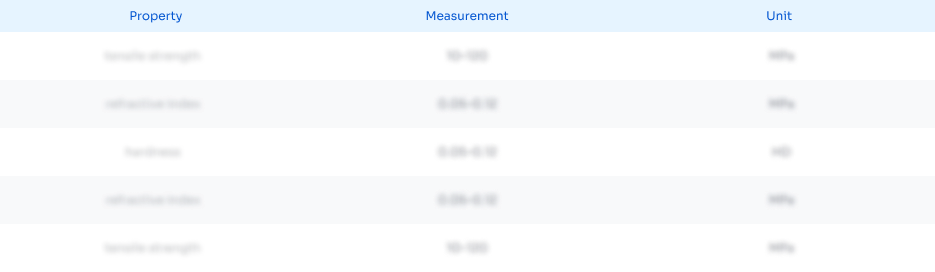
Abstract
Description
Claims
Application Information

- R&D
- Intellectual Property
- Life Sciences
- Materials
- Tech Scout
- Unparalleled Data Quality
- Higher Quality Content
- 60% Fewer Hallucinations
Browse by: Latest US Patents, China's latest patents, Technical Efficacy Thesaurus, Application Domain, Technology Topic, Popular Technical Reports.
© 2025 PatSnap. All rights reserved.Legal|Privacy policy|Modern Slavery Act Transparency Statement|Sitemap|About US| Contact US: help@patsnap.com