Multistage built-in heat source and multistage waste heat recycling type cereal drying tower
A technology of waste heat recovery and drying tower, which is applied in drying, drying machines, grain drying, etc., to achieve the effects of reducing treatment costs, reducing exhaust gas emissions, and simple structure
- Summary
- Abstract
- Description
- Claims
- Application Information
AI Technical Summary
Problems solved by technology
Method used
Image
Examples
Embodiment 1
[0036] see figure 1 , image 3 and Figure 4The second-level built-in heat source and second-level waste heat recovery type grain drying tower provided by Embodiment 1 of the present invention includes a tower body with a rectangular cross-section installed vertically on the base 21, and a feed inlet 7 is arranged on the top of the tower body. The bottom of the tower body is provided with a discharge port 23, and the inside of the tower body is sequentially provided with a grain storage section 9, a drying section 10, a drying section 2 13, a cooling section 18, a grain discharge section 20 and a grain discharge hopper 22. The feed port 7 is connected to the grain storage section 9, the discharge port 23 is connected to the grain discharge hopper 22, the grain discharge section 20 is equipped with a six-impeller type grain discharge mechanism 25, and the left side of the tower corresponding to the drying section 10 is provided with an exhaust gas chamber 3. The hot air chamb...
Embodiment 2
[0049] see figure 2 , the schematic diagram of the structure of the three-stage built-in heat source and three-stage waste heat recovery and utilization type grain drying tower provided in this embodiment, its structure is basically the same as that of Embodiment 1, the difference is that Embodiment 1 is a two-stage built-in heat source and two-stage waste heat utilization type grain drying tower. The drying tower, the second embodiment is a three-stage built-in heat source and three-stage waste heat utilization type grain drying tower, and the second embodiment has one more drying section than the first embodiment. Such as figure 2 As shown, the left side of the tower body corresponding to the drying section and the cooling section is provided with hot air chamber four 28, waste gas chamber three 5, hot air chamber one 4 and waste gas chamber one 2 from top to bottom, and the towers corresponding to the drying section and cooling section On the right side of the body, exha...
PUM
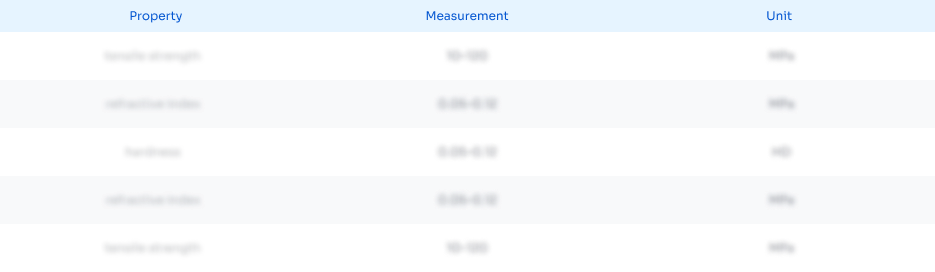
Abstract
Description
Claims
Application Information

- R&D
- Intellectual Property
- Life Sciences
- Materials
- Tech Scout
- Unparalleled Data Quality
- Higher Quality Content
- 60% Fewer Hallucinations
Browse by: Latest US Patents, China's latest patents, Technical Efficacy Thesaurus, Application Domain, Technology Topic, Popular Technical Reports.
© 2025 PatSnap. All rights reserved.Legal|Privacy policy|Modern Slavery Act Transparency Statement|Sitemap|About US| Contact US: help@patsnap.com