Production process of spunlaced non-woven fabric
A spunlace non-woven fabric and production process technology, applied in non-woven fabrics, textiles and papermaking, fiber types, etc., can solve the problems of cotton spunlace non-woven fabrics, such as hair loss, lack of water absorption, and difficult control. , to achieve the effect of reducing hair loss, long storage time, durable water absorption and washing resistance
- Summary
- Abstract
- Description
- Claims
- Application Information
AI Technical Summary
Problems solved by technology
Method used
Image
Examples
Embodiment 1
[0038] see Figure 1-5 As shown, the present embodiment is a production process of a spunlace nonwoven fabric, comprising the following steps:
[0039] Step 1: Fiber mixing: Weigh 20 parts of polyester fiber, 20 parts of bamboo fiber and 20 parts of modal fiber in parts by weight, mix them for cotton opening and cotton blending, remove dust and impurities, and mix them uniformly to obtain blended fibers;
[0040] Step 2: Carding into a web: carding with a fixed carding flat carding machine, laying a web in a cross-lapping manner through a web-laying machine, and forming a uniform blended fiber web that meets the requirements through drafting;
[0041] Step 3: Preparation of spunlaced fiber web: use high-pressure water flow to entangle the blended fiber web, and use the flat screen spunlace machine and drum spunlace machine to spunlace the front and back of the blended fiber web, and blend the fibers The net passes through the spunlace machine at a constant speed, the number o...
Embodiment 2
[0052] see Figure 1-5 As shown, the present embodiment is a production process of a spunlace nonwoven fabric, comprising the following steps:
[0053] Step 1: Fiber mixing: Weigh 25 parts of polyester fiber, 35 parts of bamboo fiber, and 35 parts of modal fiber by weight, mix them for cotton opening and cotton blending, remove dust and impurities, and mix them uniformly to obtain blended fibers;
[0054] Step 2: Carding into a web: carding with a fixed carding flat carding machine, laying a web in a cross-lapping manner through a web-laying machine, and forming a uniform blended fiber web that meets the requirements through drafting;
[0055] Step 3: Preparation of spunlaced fiber web: use high-pressure water flow to entangle the blended fiber web, and use the flat screen spunlace machine and drum spunlace machine to spunlace the front and back of the blended fiber web, and blend the fibers The net passes through the spunlace machine at a constant speed, the number of spunla...
Embodiment 3
[0066] see Figure 1-5 As shown, the present embodiment is a production process of a spunlace nonwoven fabric, comprising the following steps:
[0067] Step 1: Fiber mixing: Weigh 30 parts of polyester fiber, 50 parts of bamboo fiber and 50 parts of modal fiber in parts by weight, mix them for cotton opening and cotton blending, remove dust and impurities, and mix them uniformly to obtain blended fibers;
[0068] Step 2: Carding into a web: carding with a fixed carding flat carding machine, laying a web in a cross-lapping manner through a web-laying machine, and forming a uniform blended fiber web that meets the requirements through drafting;
[0069] Step 3: Preparation of spunlaced fiber web: use high-pressure water flow to entangle the blended fiber web, and use the flat screen spunlace machine and drum spunlace machine to spunlace the front and back of the blended fiber web, and blend the fibers The net passes through the spunlace machine at a constant speed, the number o...
PUM
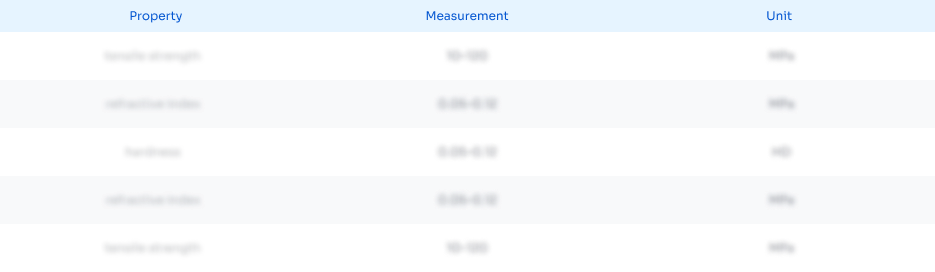
Abstract
Description
Claims
Application Information

- R&D Engineer
- R&D Manager
- IP Professional
- Industry Leading Data Capabilities
- Powerful AI technology
- Patent DNA Extraction
Browse by: Latest US Patents, China's latest patents, Technical Efficacy Thesaurus, Application Domain, Technology Topic, Popular Technical Reports.
© 2024 PatSnap. All rights reserved.Legal|Privacy policy|Modern Slavery Act Transparency Statement|Sitemap|About US| Contact US: help@patsnap.com