Thermal processing method to control the precipitation of σ phase in nodular ni-type duplex stainless steel at lower processing temperature
A duplex stainless steel, processing temperature technology, applied in the field of thermal processing of duplex stainless steel, can solve problems such as micro-cracks, lower mechanical properties and corrosion resistance of products, and unclear influence
- Summary
- Abstract
- Description
- Claims
- Application Information
AI Technical Summary
Problems solved by technology
Method used
Image
Examples
Embodiment 1
[0031] The chemical composition of the duplex stainless steel described in this example is (wt%): C: 0.036, Si: 0.25, S: 0.0028, P: 0.0058, Mn: 14.13, Cr: 23.69, Ni: 2.2, Mo: 1.29, Cu : 0.14, N: 0.28, the rest is Fe;
[0032] (1) The ingot is obtained by refining in a vacuum melting furnace, and then subjected to heat preservation at 1200°C for 2 hours to homogenize the structure;
[0033] (2) Forging the ingot, the initial forging temperature is 1100 °C, the final forging temperature is 950 °C, the forging ratio is 4, forged into a slab with a width of 130 mm and a thickness of 30 mm, and then rapidly cooled;
[0034] (3) Heat the obtained slab to 1100 °C for 1 h, then water quench to room temperature;
[0035] (4) The slab is hot-rolled, the starting rolling temperature is controlled at 1100 ℃, the final rolling temperature is kept at 980 ℃, rolled into a 12mm thick plate, and then rapidly water-cooled;
[0036] (5) Cut the rolled sheet into 20×20 mm sheets along the rolli...
Embodiment 2
[0041] The chemical composition of the duplex stainless steel described in this example is (wt%): C: 0.036, Si: 0.25, S: 0.0028, P: 0.0058, Mn: 14.13, Cr: 23.69, Ni: 2.2, Mo: 1.29, Cu : 0.14, N: 0.28, the rest is Fe.
[0042] (1) The cast ingot was obtained by refining in a vacuum melting furnace, and was homogenized at 1210 °C for 2 h;
[0043] (2) Forging the ingot, the initial forging temperature is 1150 °C, the final forging temperature is 980 °C, the forging ratio is 4.5, forged into a slab with a width of 130 mm and a thickness of 30 mm, and then rapidly cooled;
[0044] (3) Heat the obtained slab to 1120 °C, perform solution treatment for 1 h, and then water quench to room temperature;
[0045] (4) The slab is hot-rolled, the starting rolling temperature is controlled at 1120 °C, the final rolling temperature is maintained at 980 °C, rolled into a 12mm thick plate, and then rapidly water-cooled;
[0046] (5) Cut the rolled plate into 20 × 20 mm plates along the rolling ...
Embodiment 3
[0051] The chemical composition of the duplex stainless steel described in this example is (wt%): C: 0.036, Si: 0.25, S: 0.0028, P: 0.0058, Mn: 14.13, Cr: 23.69, Ni: 2.2, Mo: 1.29, Cu : 0.14, N: 0.28, and the rest is Fe.
[0052] (1) The ingot is obtained by refining in a vacuum melting furnace, and then subjected to a homogenization treatment at 1200 ℃ for 2 hours;
[0053] (2) Forging the ingot, the initial forging temperature is 1130 °C, the final forging temperature is 990 °C, the forging ratio is 5, forged into a slab with a width of 130 mm and a thickness of 30 mm, and then rapidly cooled;
[0054] (3) Heat the obtained slab to 1110 °C, perform solution treatment for 1 hour, and then water quench to room temperature;
[0055] (4) The slab is hot-rolled, the starting rolling temperature is controlled at 1080 °C, the final rolling temperature is maintained at 980 °C, rolled into a 12mm thick plate, and then rapidly water-cooled;
[0056] (5) Cut the rolled sheet into 20×...
PUM
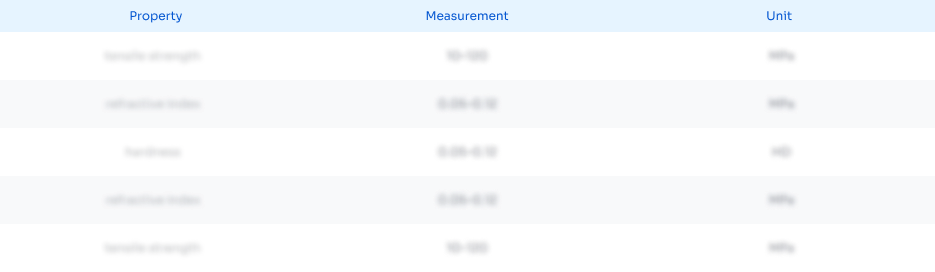
Abstract
Description
Claims
Application Information

- Generate Ideas
- Intellectual Property
- Life Sciences
- Materials
- Tech Scout
- Unparalleled Data Quality
- Higher Quality Content
- 60% Fewer Hallucinations
Browse by: Latest US Patents, China's latest patents, Technical Efficacy Thesaurus, Application Domain, Technology Topic, Popular Technical Reports.
© 2025 PatSnap. All rights reserved.Legal|Privacy policy|Modern Slavery Act Transparency Statement|Sitemap|About US| Contact US: help@patsnap.com