Punching process of sheet metal part
A technology of sheet metal parts and punching, which is applied in the field of mold manufacturing, can solve the problems of life-threatening threats to staff, reduce stamping work efficiency, etc., and achieve the effect of improving safety and processing quality of parts, improving work efficiency, and ensuring strength requirements
- Summary
- Abstract
- Description
- Claims
- Application Information
AI Technical Summary
Problems solved by technology
Method used
Image
Examples
Embodiment approach
[0032] As an embodiment of the present invention, the side wall of the cam 53 close to the bottom side of the cavity 31 is provided with a No. 1 push block 531; the cavity 31 is provided with a reinforcement unit 6; the reinforcement unit 6 includes a baffle plate 61 and a spacer 62; the baffle 61 is symmetrically fixed on the bottom side of the cavity 31 near the first plate 54, and the baffle 61 is provided with a second push block 611 near the first push block 531; the spacer 62 It is connected with the side wall of the block by a spring; the bottom end of the first plate 54 is provided with a chute plate 541; the chute plate 541 is slidably connected with a hinge rod 542; the two ends of the hinge rod 542 are hinged on the pad On the side wall of block 62; through the cooperation of No. 1 push block 531, No. 2 push block 611, baffle 61 and spacer 62, the strength of the No. 1 plate 54 and No. 2 plate 55 in the stamping process is strengthened; when working, when the mold A...
PUM
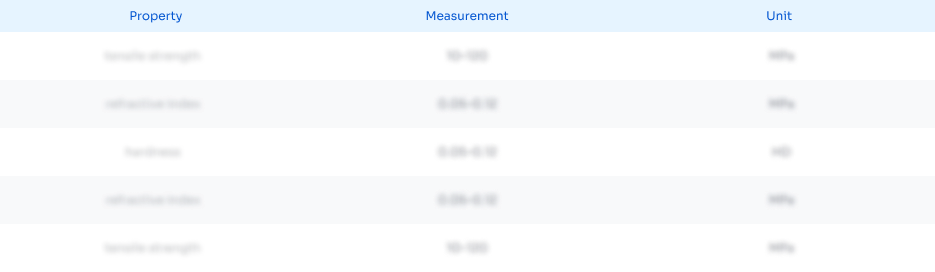
Abstract
Description
Claims
Application Information

- R&D Engineer
- R&D Manager
- IP Professional
- Industry Leading Data Capabilities
- Powerful AI technology
- Patent DNA Extraction
Browse by: Latest US Patents, China's latest patents, Technical Efficacy Thesaurus, Application Domain, Technology Topic, Popular Technical Reports.
© 2024 PatSnap. All rights reserved.Legal|Privacy policy|Modern Slavery Act Transparency Statement|Sitemap|About US| Contact US: help@patsnap.com