Bimetal composite grounding nut
A composite grounding and bi-metal technology, applied in the field of nuts in the field of transportation, can solve the problems of lack of weldability, conductivity and corrosion resistance of nuts, to ensure neatness and stability, reduce consumption, high safety and The effect of service life
- Summary
- Abstract
- Description
- Claims
- Application Information
AI Technical Summary
Problems solved by technology
Method used
Image
Examples
Embodiment 1
[0041] A method for preparing a bimetal composite ground nut, comprising the steps of:
[0042] 1) Select a 300×300×20mm stainless steel plate as the substrate 5, and a 300×300×30mm navy brass plate as the composite plate 4, respectively drill a positioning hole 6 and 8 in the four corners and the center of the opposite surface, with a diameter of 5mm, the depth is 3mm, such as figure 1 shown;
[0043] 2) Use an automatic abrasive belt grinder to remove the oxide layer and other impurities on one side to expose a clean contact surface;
[0044] 3) Use industrial alcohol to clean the surface respectively, and then blow dry;
[0045] 4) Insert the hexagonal diamond-shaped stainless steel column 7 with a diameter of 5mm and a length of 10mm into the base plate 5 and the composite plate 4 respectively, and place them on the platform 9;
[0046] 5) Place a fiberboard 3 with a thickness of 300×300×10mm on the composite board, place expanded ammonium nitrate explosives 2 evenly on t...
Embodiment 2
[0052] A method for preparing a bimetal composite ground nut, comprising the steps of:
[0053] 1) Select a 300×300×22mm aluminum alloy plate as the substrate 5, and a 300×300×28mm stainless steel plate as the composite plate 4, respectively punch a positioning hole 6 and 8 in the four corners and the center of the opposite surface, with a diameter of 5mm , the depth is 3mm, such as figure 1 shown;
[0054] 2) Use an automatic abrasive belt grinder to remove the oxide layer and other impurities on one side to expose a clean contact surface;
[0055] 3) Use industrial alcohol to clean the surface respectively, and then blow dry;
[0056] 4) Insert the hexagonal diamond-shaped stainless steel column 7 with a diameter of 5 mm and a length of 11 mm into the base plate 5 and the composite plate 4 respectively, and place them on the platform 9;
[0057] 5) Place a fiberboard 3 with a thickness of 300×300×10mm on the composite board, place expanded ammonium nitrate explosive 2 eve...
Embodiment 3
[0063] A method for preparing a bimetal composite ground nut, comprising the steps of:
[0064] 1) Select a 300×300×21mm aluminum alloy plate as the substrate 5, and a 300×300×25mm pure copper plate as the composite plate 4, respectively punch a positioning hole 6 and 8 in the four corners and the center of the opposite surface, with a diameter of 5mm , the depth is 3mm, such as figure 1 shown;
[0065] 2) Use an automatic abrasive belt grinder to remove the oxide layer and other impurities on one side to expose a clean contact surface;
[0066] 3) Use industrial alcohol to clean the surface respectively, and then blow dry;
[0067] 4) Insert the hexagonal diamond-shaped stainless steel column 7 with a diameter of 5 mm and a length of 12 mm into the base plate 5 and the composite plate 4 respectively, and place them on the platform 9;
[0068] 5) Place a fiberboard 3 with a thickness of 300×300×10mm on the composite board, place expanded ammonium nitrate explosive 2 evenly ...
PUM
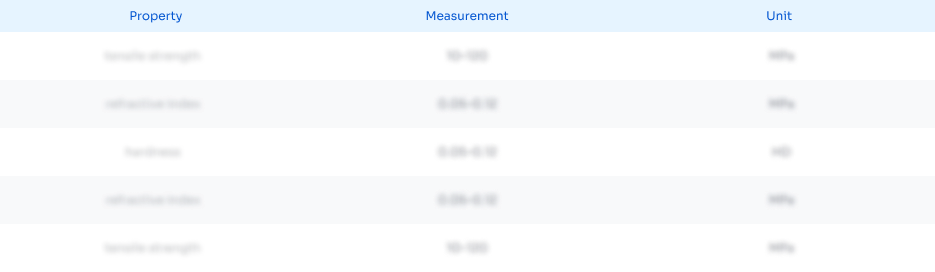
Abstract
Description
Claims
Application Information

- R&D
- Intellectual Property
- Life Sciences
- Materials
- Tech Scout
- Unparalleled Data Quality
- Higher Quality Content
- 60% Fewer Hallucinations
Browse by: Latest US Patents, China's latest patents, Technical Efficacy Thesaurus, Application Domain, Technology Topic, Popular Technical Reports.
© 2025 PatSnap. All rights reserved.Legal|Privacy policy|Modern Slavery Act Transparency Statement|Sitemap|About US| Contact US: help@patsnap.com