Method for producing latex foamed product by using low-protein latex
A foaming product and latex technology, applied in the field of latex foaming products, can solve the problems of low tensile strength, low elongation at break, uneven cell size, large compression permanent deformation, etc. Uniform size and small compression set
- Summary
- Abstract
- Description
- Claims
- Application Information
AI Technical Summary
Problems solved by technology
Method used
Examples
preparation example Construction
[0073] The second aspect of the present invention provides a method for preparing the natural latex foamed product as described above, which includes the following steps:
[0074] 1) Latex compounding: Stir and mix the formula amount of latex, additives, and vulcanizing agent for 30 minutes to obtain compounded latex for later use, and leave it to stand for 12-72 hours;
[0075] 2) Mechanical bubble: add the filler, foaming agent, and foaming agent of the formula to the compounding compound and mix, and the mixed system is stirred and foamed in the mechanical foaming machine at a speed of 200-350r / min. 5min, then reduce the speed to 50~60r / min and homogenize the foam for 1~3min; then add the active agent and stir for 0.5~2min, add the gelling agent and stir for 1~3min to obtain the styrofoam;
[0076] 3) Foam rubber injection: inject foam rubber into the mold and shape it at 95~110℃;
[0077] 4) Vulcanization: the finalized prototype is vulcanized together with the model, the temperat...
Embodiment 1
[0082] This embodiment provides a natural latex foamed product. Its raw materials, in parts by weight, include latex 100, vulcanizing agent 3, foaming agent 2.5, foaming agent 2, gelling agent 0.8, active agent 4, auxiliary Agent 8, filler 9.
[0083] The protein content of the latex is 0.65wt%; the vulcanizing agent is sulfur; the foaming agent is cetylpyridinium bromide and polyether modified organosiloxane (the viscosity at 25°C is 800~ 2000CP, purchased from Dongguan Hongya Organic Silicon Co., Ltd.), the weight ratio of which is 2.5:1; the foam stabilizer is potassium oleate; the gelling agent is sodium silicofluoride; the active agent is composed of 3 parts by weight of zinc oxide, 1 part by weight of stearic acid, 1.2 parts by weight of sodium 4-octylbenzene sulfonate, and 1 part by weight of sodium cetylbenzene sulfonate; the auxiliary agent consists of 5-10 parts by weight Vulcanization accelerator, 2-15 parts by weight of antioxidant, vulcanization accelerator is TMTD,...
Embodiment 2
[0091] This embodiment provides a natural latex foam product. The raw materials for preparation include latex 100, vulcanizing agent 5, foaming agent 6, foaming agent 5, gelling agent 1.5, active agent 3, and auxiliary materials in parts by weight. Agent 3. Filler 15.
[0092] The protein content of the latex is 0.15wt%; the vulcanizing agent is sulfur; the foaming agent is cetylpyridinium bromide and polyether modified organosiloxane (the viscosity at 25°C is 800~ 2000CP, purchased from Dongguan Hongya Organic Silicon Co., Ltd.), the weight ratio of which is 2.5:1; the foam stabilizer is potassium oleate; the gelling agent is sodium silicofluoride; the active agent is composed of 3 parts by weight of zinc oxide, 1 part by weight of stearic acid, 1.2 parts by weight of sodium 4-octylbenzene sulfonate, and 1 part by weight of sodium cetylbenzene sulfonate; the auxiliary agent consists of 5-10 parts by weight Vulcanization accelerator, 2-15 parts by weight of antioxidant, vulcaniz...
PUM
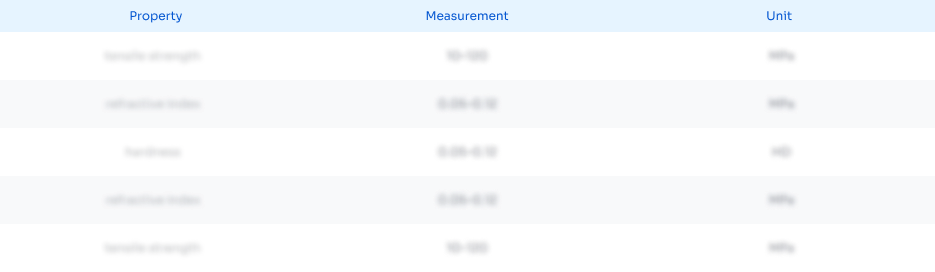
Abstract
Description
Claims
Application Information

- R&D
- Intellectual Property
- Life Sciences
- Materials
- Tech Scout
- Unparalleled Data Quality
- Higher Quality Content
- 60% Fewer Hallucinations
Browse by: Latest US Patents, China's latest patents, Technical Efficacy Thesaurus, Application Domain, Technology Topic, Popular Technical Reports.
© 2025 PatSnap. All rights reserved.Legal|Privacy policy|Modern Slavery Act Transparency Statement|Sitemap|About US| Contact US: help@patsnap.com