Method of preparing polyaspartic ester
A technology of aspartic acid ester and dibasic acid ester, which is applied in the preparation of cyanide reaction, chemical instruments and methods, and the preparation of organic compounds. It can solve the problem of slow reaction speed, high reaction temperature, and inability to directly improve the conversion of primary amine rate and other issues
- Summary
- Abstract
- Description
- Claims
- Application Information
AI Technical Summary
Problems solved by technology
Method used
Image
Examples
Embodiment 1
[0038]
[0039] (1) By mass parts, 40 parts of indium trifluoromethanesulfonate and 15 parts of indium chloride, 10 parts of copper trifluoromethanesulfonate, 5 parts of aluminum trifluoromethanesulfonate and 30 parts of aluminum oxide Disperse together in 120 parts of ethanol, stir at 55°C for 3h, distill off the solvent at 1kPa and 40°C under reduced pressure, dry the product in vacuum at 30°C for 5h, and roast it in a nitrogen atmosphere at 450°C for 3h to obtain the supported Lewis acid catalyst.
[0040] (2) Add 344.60g (2.0mol) of isophorone diamine into the 2 In the reaction kettle of the gas line pipe and the bubbler, the system was continuously purged with nitrogen and the bubbler was observed to bubble, and the stirring was started and the temperature of the reactor was controlled at 35°C, and 723.16g (4.2mol) of maleic acid di Ethyl ester was slowly and uniformly added to the reactor within 2 hours. After the addition was complete, 2.76 g of supported Lewis acid c...
Embodiment 2
[0044]
[0045] (1) By mass parts, 45 parts of indium trifluoromethanesulfonate and 13 parts of indium chloride, 8 parts of copper trifluoromethanesulfonate, 5 parts of aluminum trifluoromethanesulfonate and 29 parts of aluminum oxide Disperse together in 150 parts of ethanol, stir at 60°C for 3.5h, distill and remove the solvent under reduced pressure at 1kPa at 40°C, dry the product in vacuum at 40°C for 3h, then roast at 500°C for 3h in a nitrogen atmosphere to obtain a supported type Lewis acid catalyst.
[0046] (2) Add 420.72g (2.0mol) 4,4'-diaminodicyclohexylmethane into the 2 In the reaction kettle of the gas line pipe and the bubbler, the system was continuously purged with nitrogen and the bubbler was observed to bubble, and the stirring was started and the temperature of the reactor was controlled at 40°C, and 723.16g (4.2mol) of maleic acid di Ethyl ester was slowly and uniformly added to the reactor within 2 hours. After the addition was completed, 5.05 g of s...
Embodiment 3
[0050]
[0051] (1) By mass parts, 60 parts of indium trifluoromethanesulfonate and 5 parts of indium chloride, 8 parts of copper trifluoromethanesulfonate, 7 parts of aluminum trifluoromethanesulfonate and 20 parts of aluminum oxide Disperse together in 200 parts of ethanol, stir at 60°C for 4h, distill off the solvent at 1kPa, 40°C under reduced pressure, dry the product in vacuum at 50°C for 5h, and roast it in a nitrogen atmosphere at 550°C for 4h to obtain the supported Lewis acid catalyst.
[0052] (2) Add 476.82g (2.0mol) 3,3'-dimethyl-4,4'-diaminodicyclohexylmethane into the 2 In the reaction kettle of the gas line pipe and the bubbler, the system was continuously purged with nitrogen and the bubbler was observed to bubble, and the stirring was started and the temperature of the reactor was controlled at 50°C, and 723.16g (4.2mol) of maleic acid di Ethyl ester was slowly and uniformly added to the reactor within 2 hours. After the addition was completed, 23.84 g of...
PUM
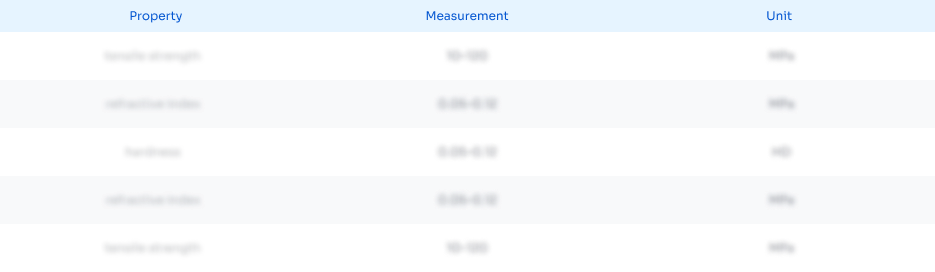
Abstract
Description
Claims
Application Information

- R&D Engineer
- R&D Manager
- IP Professional
- Industry Leading Data Capabilities
- Powerful AI technology
- Patent DNA Extraction
Browse by: Latest US Patents, China's latest patents, Technical Efficacy Thesaurus, Application Domain, Technology Topic, Popular Technical Reports.
© 2024 PatSnap. All rights reserved.Legal|Privacy policy|Modern Slavery Act Transparency Statement|Sitemap|About US| Contact US: help@patsnap.com