Manufacturing method of long-service-life forged aluminum alloy wheel
A manufacturing method and technology of aluminum alloy, applied in vehicle parts, transportation and packaging, etc., can solve the problems of short life, high cost, easy corrosion and oxidation, etc., and achieve the effect of increasing hardness, prolonging service life and good corrosion resistance
- Summary
- Abstract
- Description
- Claims
- Application Information
AI Technical Summary
Problems solved by technology
Method used
Image
Examples
Embodiment 1
[0030] Such as Figure 1 to Figure 2 Shown, a kind of long-life forged aluminum alloy wheel manufacturing method comprises the following steps:
[0031] S1: Bar stock heating: 6061 aluminum bars are heated in the bar stock heating furnace for 110 minutes, and the bar stock exit temperature is 460°C;
[0032] S2: Forging: On a 6,000-ton press, the temperature of the forging die is 370°C, and the heated bar is forged in a single step to produce a round forging billet with rim legs;
[0033] S3: Punching and flaring: On the 315t press, place the rim leg of the forged billet upwards, use the flaring block to expand the rim leg to a certain angle, and at the same time punch the center of the forging billet to facilitate the subsequent spinning process forging The blank is placed on the spinning die and the blank is positioned.
[0034] S4: Cleaning and cooling: After the flaring and punching, the forged blank enters the cleaning line and is cleaned with room temperature water;
...
Embodiment 2
[0043] A method for manufacturing a long-life forged aluminum alloy wheel, comprising the following steps:
[0044] S1: Bar stock heating: 6061 aluminum bars are heated in the bar stock heating furnace for 120 minutes, and the bar stock exit temperature is 480°C;
[0045]S2: Forging: On a 6,000-ton press, the temperature of the forging die is 380°C, and the heated bar is forged in a single step to produce a round forging billet with rim legs;
[0046] S3: Punching and flaring: On the 315t press, place the rim leg of the forged billet upwards, use the flaring block to expand the rim leg to a certain angle, and punch the center of the forged billet with the punch;
[0047] S4: Cleaning and cooling: After the flaring and punching, the forged blank enters the cleaning line and is cleaned with room temperature water;
[0048] S5: Spinning: Put the cleaned flaring forging billet on the spinning lower die, and the tail top will compact the forging billet. During the spinning process...
Embodiment 3
[0056] A method for manufacturing a long-life forged aluminum alloy wheel, comprising the following steps:
[0057] S1: Bar stock heating: 6061 aluminum bar is heated in the bar stock heating furnace for 100 minutes, and the bar stock exit temperature is 506°C;
[0058] S2: Forging: On a 6,000-ton press, the temperature of the forging die is 390°C, and the heated bar is forged in a single step to produce a round forging billet with rim legs;
[0059] S3: Punching and flaring: On the 315t press, place the rim leg of the forged billet upwards, use the flaring block to expand the rim leg to a certain angle, and punch the center of the forged billet with the punch;
[0060] S4: Cleaning and cooling: After the flaring and punching, the forged blank enters the cleaning line and is cleaned with room temperature water;
[0061] S5: Spinning: Put the cleaned flaring forging billet on the spinning lower die, and the tail top will compact the forging billet. During the spinning process,...
PUM
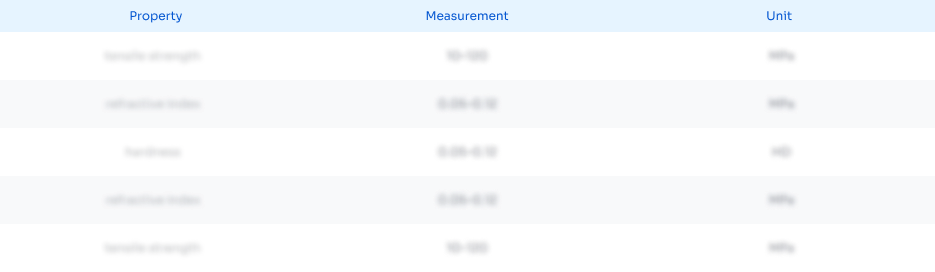
Abstract
Description
Claims
Application Information

- R&D
- Intellectual Property
- Life Sciences
- Materials
- Tech Scout
- Unparalleled Data Quality
- Higher Quality Content
- 60% Fewer Hallucinations
Browse by: Latest US Patents, China's latest patents, Technical Efficacy Thesaurus, Application Domain, Technology Topic, Popular Technical Reports.
© 2025 PatSnap. All rights reserved.Legal|Privacy policy|Modern Slavery Act Transparency Statement|Sitemap|About US| Contact US: help@patsnap.com