Improved diagnosis method for complex faults of rotating machinery with deep sparse autoencoder network
A technology of sparse autoencoder and rotating machinery, which is applied in neural learning methods, biological neural network models, and testing of machine/structural components. Composite fault diagnosis, misdiagnosis and missed diagnosis, etc., achieve the advantages of monitoring and diagnosis ability and generalization ability, get rid of the dependence of signal processing knowledge and diagnosis engineering experience, and the effect of strong generalization ability
- Summary
- Abstract
- Description
- Claims
- Application Information
AI Technical Summary
Problems solved by technology
Method used
Image
Examples
Embodiment Construction
[0075] The specific implementation of the present invention will be further described in detail below in conjunction with the accompanying drawings, attached tables and examples.
[0076] In order to make up for the deficiencies in the prior art, the present invention is based on the relationship constraint item and the improved deep sparse autoencoder network rotating machinery compound fault diagnosis method, firstly establishes the relationship constraint item that alleviates the correlation between data, and adopts the improved deep sparse autoencoder network The self-encoder network is used to learn the essential characteristics of the training sample data; then the softmax classifier is used to classify and identify the test samples, so as to determine the category of the composite fault condition of the rotating machinery and the severity of the fault, so as to improve the accuracy of the composite fault diagnosis of the rotating machinery , Adaptability, Effectiveness a...
PUM
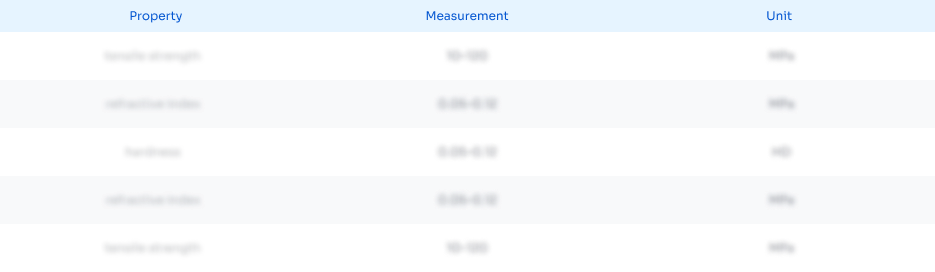
Abstract
Description
Claims
Application Information

- R&D
- Intellectual Property
- Life Sciences
- Materials
- Tech Scout
- Unparalleled Data Quality
- Higher Quality Content
- 60% Fewer Hallucinations
Browse by: Latest US Patents, China's latest patents, Technical Efficacy Thesaurus, Application Domain, Technology Topic, Popular Technical Reports.
© 2025 PatSnap. All rights reserved.Legal|Privacy policy|Modern Slavery Act Transparency Statement|Sitemap|About US| Contact US: help@patsnap.com