A magnetorheological fluid flexible clamping device and method for blade parts
A magnetorheological fluid and flexible clamping technology, applied in the field of parts clamping, can solve problems such as affecting machining accuracy, blade fatigue strength drop, blade fracture, etc., to ensure support reliability, machining accuracy, and support rigidity. Effect
- Summary
- Abstract
- Description
- Claims
- Application Information
AI Technical Summary
Problems solved by technology
Method used
Image
Examples
Embodiment Construction
[0016] The embodiments of the present invention will be described in detail in conjunction with the drawings and technical solutions.
[0017] The blade 8 is a high-temperature alloy GH4196 sheet material, the thickness after rolling is 0.8mm, the total length of the blade is 150mm, the final surface roughness is 0.4, and the minimum work difference of the airfoil profile is +0.03~-0.03mm. Carbonyl iron powder magnetorheological fluid is made of 40% volume fraction of carbonyl iron powder and 60% volume fraction of silicone oil, with a density of 3.55g / ml. The maximum thickness of magnetorheological fluid is 14mm. Grinding force 100N. The magnetic field strength is greater than 120A / m.
[0018] attached figure 1 It is the overall schematic diagram of the magnetorheological fluid flexible clamping device for processing blade parts. The magnetorheological flexible clamping device in the figure is composed of tenon magnetorheological clamping mechanism Ⅰ, blade body magnetorhe...
PUM
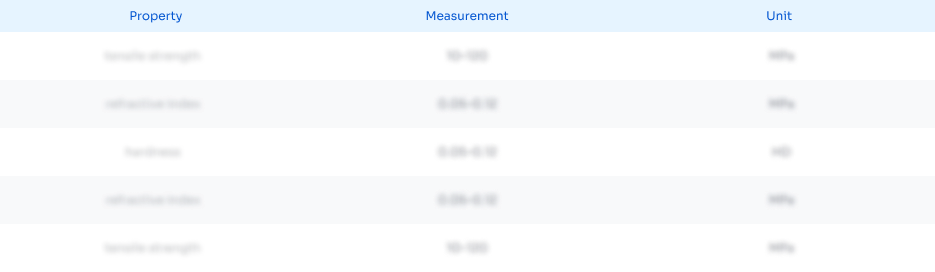
Abstract
Description
Claims
Application Information

- Generate Ideas
- Intellectual Property
- Life Sciences
- Materials
- Tech Scout
- Unparalleled Data Quality
- Higher Quality Content
- 60% Fewer Hallucinations
Browse by: Latest US Patents, China's latest patents, Technical Efficacy Thesaurus, Application Domain, Technology Topic, Popular Technical Reports.
© 2025 PatSnap. All rights reserved.Legal|Privacy policy|Modern Slavery Act Transparency Statement|Sitemap|About US| Contact US: help@patsnap.com