Self-polishing antifouling anticorrosive coating for submarine cables
A technology for submarine cables and anti-corrosion coatings, applied in anti-corrosion coatings, anti-fouling/underwater coatings, coatings, etc., can solve problems such as short service life, inability to protect submarine cables, poor adhesion performance, etc., and achieve anti-shear rate , Remarkable drag reduction effect, good retarding performance
- Summary
- Abstract
- Description
- Claims
- Application Information
AI Technical Summary
Problems solved by technology
Method used
Image
Examples
Embodiment 1
[0018] A self-polishing submarine cable anti-fouling and anti-corrosion coating, the preparation method thereof comprises the following steps: 1. Weigh each raw material according to the proportion, transfer vinyl ester resin preheated to 60°C into a reaction kettle, and raise the temperature of the reaction kettle When the temperature reaches about 90°C, add azobisisobutyronitrile and keep the temperature constant for 20 minutes; raise the temperature of the reactor to 120°C, and drop a certain amount of 2-acrylamide-2-methylpropanesulfonic acid slowly within 1 hour with a dropping funnel Aqueous solution, N-acryloylmorpholine, and acetic acid aqueous solution, after adding, add mercaptoethanol under nitrogen atmosphere, keep the temperature for 30 minutes, stop the reaction, and obtain modified vinyl ester resin; 2. Mix phthalic anhydride and dicyclopentan Put the diene into another reaction kettle, raise the temperature, stir, blow nitrogen, and drop pure water at 140°C for ...
Embodiment 2
[0025]A self-polishing submarine cable anti-fouling and anti-corrosion coating. The preparation method comprises the following steps: 1. Weigh each raw material according to the proportion, transfer vinyl ester resin preheated to 50-60°C into a reaction kettle, and react When the temperature of the kettle rises to about 90°C, add azobisisobutyronitrile and keep the temperature constant for 20 minutes; raise the temperature of the reactor to 120°C, and slowly add a certain amount of 2-acrylamide-2-methylpropane dropwise within 1 hour with a dropping funnel Sulfonic acid aqueous solution, N-acryloylmorpholine, and acetic acid aqueous solution, after adding, add mercaptoethanol under nitrogen atmosphere, then keep the temperature for 30 minutes, stop the reaction, and obtain modified vinyl ester resin; 2. Mix phthalic anhydride and Add dicyclopentadiene into another reaction kettle, heat up, stir, blow nitrogen, add pure water dropwise at 135°C for about 30-60 minutes, and keep wa...
PUM
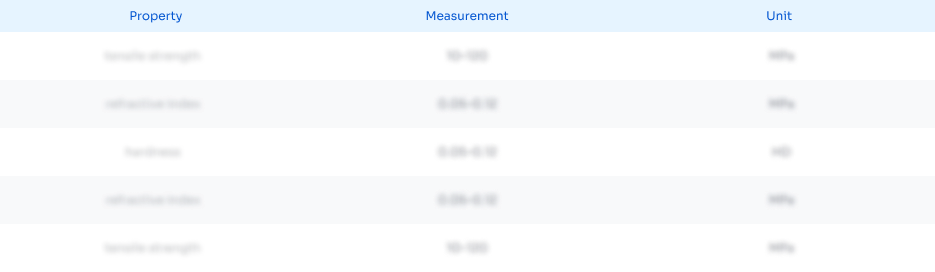
Abstract
Description
Claims
Application Information

- R&D Engineer
- R&D Manager
- IP Professional
- Industry Leading Data Capabilities
- Powerful AI technology
- Patent DNA Extraction
Browse by: Latest US Patents, China's latest patents, Technical Efficacy Thesaurus, Application Domain, Technology Topic, Popular Technical Reports.
© 2024 PatSnap. All rights reserved.Legal|Privacy policy|Modern Slavery Act Transparency Statement|Sitemap|About US| Contact US: help@patsnap.com