Lignocellulose pretreatment method and application thereof in a fluid shear-driven urea/alkali system
A lignocellulose and fluid shearing technology, which is applied in the fields of biomass resource utilization and agricultural waste comprehensive utilization, can solve the problems of solution instability, little industrial significance, and insufficient solvency, so as to increase porosity and enhance Effect of Enzymatic Hydrolysis Efficiency and Chemical Catalytic Conversion Efficiency
- Summary
- Abstract
- Description
- Claims
- Application Information
AI Technical Summary
Problems solved by technology
Method used
Image
Examples
Embodiment 1
[0034]12wt% urea / 7wt% sodium hydroxide aqueous solution was pre-cooled to -12°C. Pass the beech wood powder through a 60-mesh sieve, put it in an oven at 50°C and dry it for 24 hours to constant weight. After dry milling for 15 minutes, take 20g of wood powder and add it to the pre-cooled urea / alkali aqueous solution to prepare a mixed solution, the solid-to-liquid ratio is 1:10, and after stirring, put it into a high-speed homogenizer (Jieshi 100-Y) for fluidization Shearing (rotating speed is 49000r / min) for 20min. Freeze the mixture at -20°C for 12 hours, then continue to shear for 10 minutes, accumulatively shearing for 30 minutes. Solid-liquid separation is performed on the pretreated mixed liquid, and the collected solid residue is washed with water until neutral, which is the lignocellulose pretreated product S1 and the supernatant liquid L1. Add conc . The determination of cellulose, hemicellulose, lignin and soluble sugar in biomass is based on the standard determ...
Embodiment 2
[0039] Beech wood flour is passed through a 60-mesh sieve, put into an oven at 50°C for 24 hours to constant weight, and after 15 minutes of dry grinding, take 20g of wood flour and 12wt% urea / 7wt% sodium hydroxide aqueous solution to prepare a mixed solution, the solid-to-liquid ratio The ratio is 1:10, pre-cooled to -12°C after stirring, and placed in a high-speed homogenizer (Jieshi 100-Y) for fluid shearing (49000r / min) for 10min. Freeze the mixture at -20°C for 12 hours, then continue to shear for 20 minutes, accumulatively shearing for 30 minutes. Solid-liquid separation is performed on the pretreated mixed liquid, and the collected solid residue is washed with water until neutral, which is the lignocellulose pretreated product S1 and the supernatant liquid L1. Add conc . The content of L2 carbohydrates in the supernatant was detected by high performance liquid chromatography. The temperature of the whole pretreatment process does not exceed 60°C.
[0040] The result...
Embodiment 3
[0044] Beech wood flour is passed through a 60-mesh sieve, put into an oven at 50°C for 24 hours to constant weight, and after 15 minutes of dry grinding, take 20g of wood flour and 12wt% urea / 7wt% sodium hydroxide aqueous solution to prepare a mixed solution, the solid-to-liquid ratio The ratio is 1:10, pre-cooled to -12°C after stirring, and placed in a high-speed homogenizer (Jieshi 100-Y) for fluid shearing (49000r / min) for 30min. Solid-liquid separation is performed on the pretreated mixed liquid, and the collected solid residue is washed with water until neutral, which is the lignocellulose pretreated product S1 and the supernatant liquid L1. Add conc . The content of L2 carbohydrates in the supernatant was detected by high performance liquid chromatography. The temperature of the whole pretreatment process does not exceed 60°C.
[0045] The results show that the pretreated material S2 contains the following components (calculated by mass fraction): dextran (8.7%), xy...
PUM
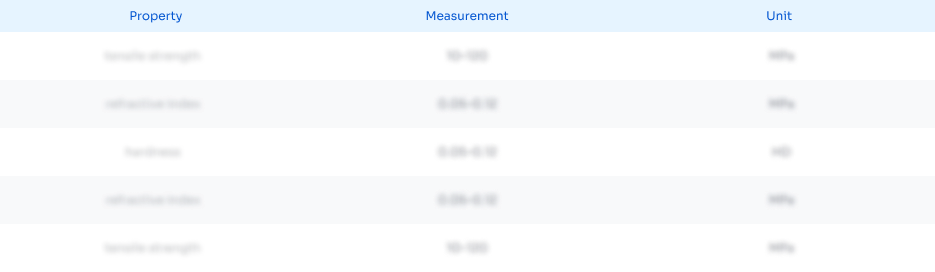
Abstract
Description
Claims
Application Information

- R&D Engineer
- R&D Manager
- IP Professional
- Industry Leading Data Capabilities
- Powerful AI technology
- Patent DNA Extraction
Browse by: Latest US Patents, China's latest patents, Technical Efficacy Thesaurus, Application Domain, Technology Topic, Popular Technical Reports.
© 2024 PatSnap. All rights reserved.Legal|Privacy policy|Modern Slavery Act Transparency Statement|Sitemap|About US| Contact US: help@patsnap.com