Preparation method for copper-indium-gallium alloy powder
A technology of copper indium gallium alloy and copper indium gallium, which is applied in the field of alloy powder manufacturing, can solve the problems of increasing energy consumption cost and production cost, prolonging the preparation cycle of alloy powder, and burning loss of low melting point metal elements, so as to reduce energy consumption cost , Extensive use of value, the effect of reducing waste
- Summary
- Abstract
- Description
- Claims
- Application Information
AI Technical Summary
Problems solved by technology
Method used
Image
Examples
preparation example Construction
[0032] According to some preferred embodiments of the present invention, the preparation method of copper indium gallium alloy powder includes:
[0033] Copper, indium, gallium, and recovered copper indium gallium alloy powders whose particle size is not within the set range are smelted into an alloy solution in a melting crucible. In this smelting step, indium and gallium are placed at the bottom of the melting crucible, and the copper particles are Mix it with the recovered copper indium gallium powder whose particle size is not within the set range and place it above the indium and gallium in the smelting crucible;
[0034] Atomizing, cooling, and sieving the alloy solution to obtain copper indium gallium alloy powder with a particle size within a set range;
[0035] Copper indium gallium alloy powder whose particle size is not within the set range is recovered.
[0036] The metal copper material needs to use granular materials, copper of equal quality, the smaller the par...
Embodiment approach
[0044] According to some preferred embodiments of the present invention, the atomized pulverization process includes:
[0045] Pour the alloy solution into the preheated tundish;
[0046] Introduce atomized gas for powder making operation;
[0047] Sieve to collect copper indium gallium alloy powder with a particle size within a set range;
[0048] Copper indium gallium alloy powder whose particle size is not within the set range is recovered.
[0049] According to some preferred embodiments of the present invention, the preheating temperature is 750-770°C.
[0050] According to some preferred embodiments of the present invention, the atomizing gas is nitrogen, argon, helium, the pressure is 2MPa-2.5Mpa, and the gas flow rate is 18kg / min-20kg / min.
[0051] According to the copper indium gallium alloy powder obtained by the above method of the present invention, the proportion of copper indium gallium in its composition is: (20%-50%): (15%-40%): (5%-30%) (by mass count). The...
Embodiment 1
[0072] As shown in Example 1 in Table 1, 26 kg of copper particles with a size of 10 mm are used, which are fully mixed with 65 kg of CIG alloy powder with a particle size of less than 38 μm and greater than 150 μm in advance, and then as figure 1 As shown in middle 2, indium and gallium are placed at the bottom of the melting crucible 1, and the above-mentioned copper particles and CIG mixture are placed as figure 1 3 is placed above the indium and gallium in the melting crucible 1 . Among them, the feeding ratio of copper, indium and gallium is 40%: 40%: 20%, the melting temperature is 915°C, the vacuum degree is 0.2mbar, all metals can be completely alloyed in 51 minutes of melting, and the pouring temperature is 810±10 ℃, the tundish temperature is 760±10℃, the nitrogen pressure is 2±0.05Mpa, and the nitrogen flow rate is 19.2±0.2. The composition detection results of the obtained CIG alloy powder are 39.83%, 40.13%, and 20.04% for copper, indium, and gallium, respectivel...
PUM
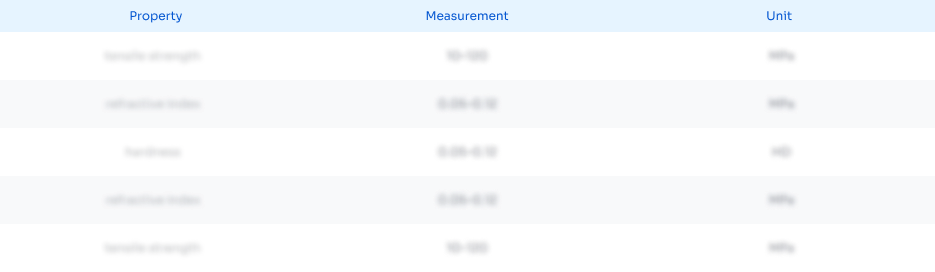
Abstract
Description
Claims
Application Information

- R&D
- Intellectual Property
- Life Sciences
- Materials
- Tech Scout
- Unparalleled Data Quality
- Higher Quality Content
- 60% Fewer Hallucinations
Browse by: Latest US Patents, China's latest patents, Technical Efficacy Thesaurus, Application Domain, Technology Topic, Popular Technical Reports.
© 2025 PatSnap. All rights reserved.Legal|Privacy policy|Modern Slavery Act Transparency Statement|Sitemap|About US| Contact US: help@patsnap.com