Preparation method of acrylic resin for flexible plastics
A technology of acrylic resin and flexible plastic, which is applied in the field of resin to achieve the effect of improving flexibility, increasing reaction and good hydrolysis resistance
- Summary
- Abstract
- Description
- Claims
- Application Information
AI Technical Summary
Problems solved by technology
Method used
Image
Examples
Embodiment 1
[0021] (1) First, put caprolactone and hydroxyethyl acrylate in an equimolar ratio into the reaction kettle, feed N2 protection to start stirring, and raise the temperature to 140-150°C to maintain this temperature;
[0022] (2) add an appropriate amount of organotin catalyst, maintain at this temperature for 5 hours, lower the temperature and cool down, and obtain intermediate B;
[0023] (3) 10% intermediate B, 8% (meth)methyl acrylate, 25% butyl methacrylate, 9% styrene, 9.5% hydroxyethyl acrylate, 0.8% acrylic acid, 3% initiator, Throw it into the high-level tank to dissolve safely and stir evenly;
[0024] (4) Add 35% xylene into the reaction kettle, raise the temperature to 130±2°C, drop the monomer in the head tank into the reaction kettle at a constant speed for 3 hours, keep it for 1 hour, add the initiator, and keep it for another 2 hours, and check the acid value of the resin , viscosity, and pass the test, dilute it with xylene to the required solid content, cool ...
Embodiment 2
[0026] (1) First, put caprolactone and hydroxyethyl acrylate in an equimolar ratio into the reaction kettle, feed N2 protection to start stirring, and raise the temperature to 140-150°C to maintain this temperature;
[0027] (2) add an appropriate amount of organotin catalyst, maintain at this temperature for 5 hours, lower the temperature and cool down, and obtain intermediate B;
[0028] (3) 15% intermediate B, 8.2% (meth)methyl acrylate, 22% butyl methacrylate, 10% styrene, 8% hydroxyethyl acrylate, 1.3% acrylic acid, 2.5% initiator, Throw it into the high-level tank to dissolve safely and stir evenly;
[0029] (4) Add 33% xylene into the reaction kettle, raise the temperature to 130±2°C, drop the monomer in the head tank into the reaction kettle at a constant speed for 3 hours, keep it for 1 hour, add the initiator, and keep it for another 2 hours, and check the acid value of the resin , viscosity, and pass the test, dilute it with xylene to the required solid content, co...
PUM
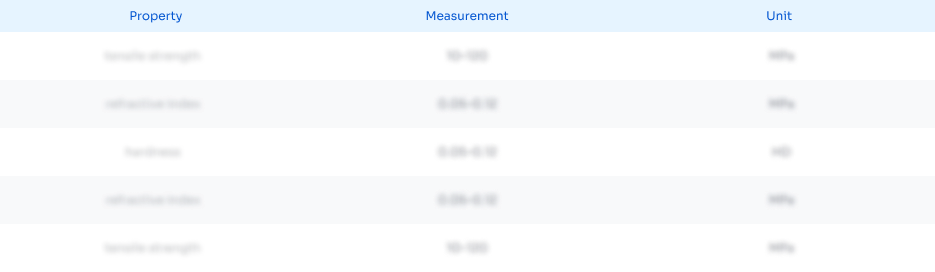
Abstract
Description
Claims
Application Information

- R&D
- Intellectual Property
- Life Sciences
- Materials
- Tech Scout
- Unparalleled Data Quality
- Higher Quality Content
- 60% Fewer Hallucinations
Browse by: Latest US Patents, China's latest patents, Technical Efficacy Thesaurus, Application Domain, Technology Topic, Popular Technical Reports.
© 2025 PatSnap. All rights reserved.Legal|Privacy policy|Modern Slavery Act Transparency Statement|Sitemap|About US| Contact US: help@patsnap.com