Method for removing carbon from nitride powder
A nitride and powder technology, applied in nitrogen compounds, chemical instruments and methods, inorganic chemistry, etc., can solve problems such as poor carbon removal effect, and achieve the effect of excellent performance
- Summary
- Abstract
- Description
- Claims
- Application Information
AI Technical Summary
Problems solved by technology
Method used
Image
Examples
Embodiment 1
[0024] The method for removing carbon from the nitride powder described in this embodiment comprises the following steps:
[0025] (1) Put 50 g of aluminum nitride powder with a carbon content of 18% obtained by sintering by carbothermal reduction into a corundum crucible, put the corundum crucible into a microwave oven, adjust the power of the microwave oven to 700W, and heat for 60 minutes ;
[0026] (2) After the microwave oven was naturally cooled to room temperature, the sample was transferred to a muffle furnace, and the temperature was raised to 650° C. under air conditions for 5 hours of heat preservation and roasting to obtain aluminum nitride powder.
Embodiment 2
[0028] The method for removing carbon from the nitride powder described in this embodiment comprises the following steps:
[0029] (1) Put 50 g of aluminum nitride powder with a carbon content of 18% obtained by sintering by carbothermal reduction into a corundum crucible, put the corundum crucible into a microwave oven, adjust the power of the microwave oven to 500W, and heat for 120 minutes ;
[0030] (2) After the microwave oven was naturally cooled to room temperature, the sample was transferred to a muffle furnace, and the temperature was raised to 600° C. under air conditions for 10 hours of heat preservation and roasting to obtain aluminum nitride powder.
Embodiment 3
[0032] The method for removing carbon from the nitride powder described in this embodiment comprises the following steps:
[0033] (1) Put 50g of aluminum nitride powder with a carbon content of 10% obtained by sintering by carbothermal reduction into a corundum crucible, put the corundum crucible into a microwave oven, adjust the power of the microwave oven to 1100W, and heat for 20 minutes ;
[0034] (2) After the microwave oven was naturally cooled to room temperature, the sample was transferred to a muffle furnace, and the temperature was raised to 600° C. under the condition of pure oxygen for 10 hours of heat preservation and roasting to obtain aluminum nitride powder.
PUM
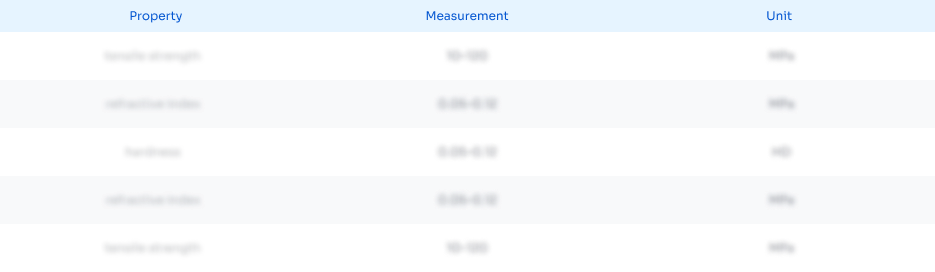
Abstract
Description
Claims
Application Information

- R&D
- Intellectual Property
- Life Sciences
- Materials
- Tech Scout
- Unparalleled Data Quality
- Higher Quality Content
- 60% Fewer Hallucinations
Browse by: Latest US Patents, China's latest patents, Technical Efficacy Thesaurus, Application Domain, Technology Topic, Popular Technical Reports.
© 2025 PatSnap. All rights reserved.Legal|Privacy policy|Modern Slavery Act Transparency Statement|Sitemap|About US| Contact US: help@patsnap.com