All-position automatic welding technology applied to pipeline joint of vehicle liquefied natural gas cylinder
A liquefied natural gas and automatic welding technology, which is applied in welding equipment, arc welding equipment, manufacturing tools, etc., can solve the problems of difficult to guarantee welding quality, low welding efficiency, high welder skill requirements, etc., and achieve high welding efficiency, small heat input, High quality of weld seam and its consistent effect
- Summary
- Abstract
- Description
- Claims
- Application Information
AI Technical Summary
Problems solved by technology
Method used
Image
Examples
Embodiment 1
[0038] figure 1 It is a technical explanatory drawing of the all-position automatic welding technology for the pipeline joints of liquefied natural gas cylinders for vehicles. The all-position automatic welding device includes a support 1, a gear 2, a tungsten electrode 3, a fixture a5, a fixture b6, a connecting wire 8 and a welding power source 9.
[0039] Fixture a5 is fixed on the welding side of the joint 4, fixture b6 is fixed on the welding side of the pipeline 7, supports 1 are fixed on both sides of the fixture a5 and fixture b6, and the supports 1 are arranged at intervals; gears 2 are arranged at the intervals of the supports 1, The tungsten pole 3 is installed on the gear 1 , the protruding height of the tungsten pole 3 can be adjusted, and the rotation angle of the tungsten pole 3 is 375°-385°; one end of the gear 2 is electrically connected to the welding power source 9 via the connecting wire 8 .
[0040] The overall curved surfaces of the joint 4 and the pipel...
Embodiment 2
[0046]The all-position automatic welding technology is used for the pipeline joints of liquefied natural gas cylinders for vehicles, including: support 1, inner hole fixtures for fixing pipelines 7 and joints 4, tungsten poles 3 and gears 2 for installing tungsten poles 3, and welding power supply 9. Pulse current is used, and the welding parameters are divided into four intervals. The high current melts the metal welding of the welding object, and the low current maintains the arc and cools the weld; 7. The tungsten electrode 3 is centered on the end face of the joint 4 with no wire filling, and the welding object is fixed. The tungsten electrode 3 rotates along the welding object for one circle to complete the welding. There is no need for spot welding before welding, and it is passed into the back of the weld. Argon gas protection; when the pipeline 7 is a bent pipe, the all-position automatic welding of the joint 4 and the curved pipeline 7 can be realized by making an inne...
PUM
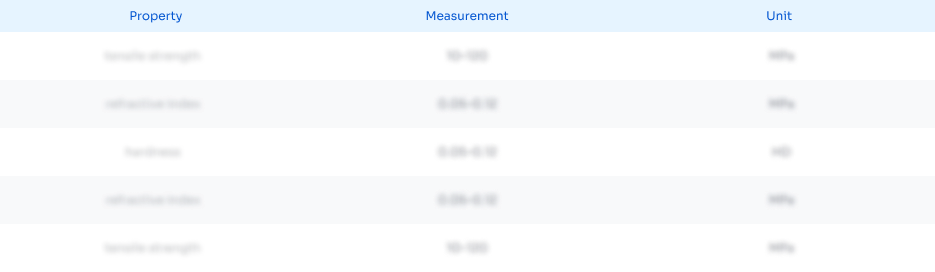
Abstract
Description
Claims
Application Information

- R&D
- Intellectual Property
- Life Sciences
- Materials
- Tech Scout
- Unparalleled Data Quality
- Higher Quality Content
- 60% Fewer Hallucinations
Browse by: Latest US Patents, China's latest patents, Technical Efficacy Thesaurus, Application Domain, Technology Topic, Popular Technical Reports.
© 2025 PatSnap. All rights reserved.Legal|Privacy policy|Modern Slavery Act Transparency Statement|Sitemap|About US| Contact US: help@patsnap.com