Method for preparing MgZn2, Zn and oxide three-layer antiseptic films on surfaces of magnesium alloys
An oxide film, three-layer anti-corrosion technology, applied in the direction of metal material coating process, coating, ion implantation plating, etc., can solve the problems of limitation and poor corrosion resistance, and achieve the effect of preventing contact
- Summary
- Abstract
- Description
- Claims
- Application Information
AI Technical Summary
Problems solved by technology
Method used
Image
Examples
Embodiment 1
[0023] (1) AM50 magnesium alloy pretreatment method, after cutting the magnesium alloy into a size of 10mm×10mm×1mm, grinding and polishing with SiC sandpaper of No. 600 and No. 1000 respectively, first remove the surface oil with an alkaline degreaser, Reuse 85% H 3 PO 4 Etch for 30-40s, remove the surface oxide film, wash with distilled water and soak in absolute ethanol for later use;
[0024] (2) Put the pretreated magnesium alloy into a vacuum evaporation device and evacuate until the vacuum degree is better than 1×10 - 3 After MPa, the zinc particles are heated to 350°C, and the zinc vapor condenses on the surface of the magnesium alloy to form a zinc film;
[0025] (3) Put the magnesium alloy after evaporating zinc into the quartz tube, vacuumize the quartz tube and seal it. Put the quartz tube into a box furnace and anneal at 250°C for 2 hours;
[0026] (4) packing the magnesium alloy after the annealing in the quartz tube with the homogeneous mixture of the high-...
Embodiment 2
[0029](1) AZ91D magnesium alloy pretreatment method, after cutting the magnesium alloy into a size of 10mm×10mm×1mm, grinding and polishing with SiC sandpaper of No. 600 and No. 1000 respectively, first remove the surface oil with an alkaline degreaser, Reuse 85% H 3 PO 4 Etch for 30-40s, remove the surface oxide film, wash with distilled water and soak in absolute ethanol for later use;
[0030] (2) Put the pretreated magnesium alloy into a vacuum evaporation device and evacuate until the vacuum degree is better than 1×10 - 3 After MPa, the zinc particles are heated to 400°C, and the zinc vapor condenses on the surface of the magnesium alloy to form a zinc film;
[0031] (3) Put the magnesium alloy after evaporating zinc into the quartz tube, vacuumize the quartz tube and seal it. Put the quartz tube into a box furnace and anneal at 300°C for 2 hours;
[0032] (4) packing the magnesium alloy after the annealing in the quartz tube with the homogeneous mixture of the high-...
Embodiment 3
[0035] (1) ZK61S magnesium alloy pretreatment method, after cutting the magnesium alloy into a size of 10mm×10mm×1mm, grinding and polishing with SiC sandpaper of No. 600 and No. 1000 respectively, first remove the surface oil with an alkaline degreaser, Reuse 85% H 3 PO 4 Etch for 30-40s, remove the surface oxide film, wash with distilled water and soak in absolute ethanol for later use;
[0036] (2) Put the pretreated magnesium alloy into a vacuum evaporation device and evacuate until the vacuum degree is better than 1×10 - 3 After MPa, the zinc particles are heated to 500°C, and the zinc vapor condenses on the surface of the magnesium alloy to form a zinc film;
[0037] (3) Put the magnesium alloy after evaporating zinc into the quartz tube, vacuumize the quartz tube and seal it. Put the quartz tube into a box furnace and anneal at 350°C for 2 hours;
[0038] (4) Pack the homogeneous mixture of high-purity powders of 875mgFe and 1125mgFeO and the magnesium alloy after ...
PUM
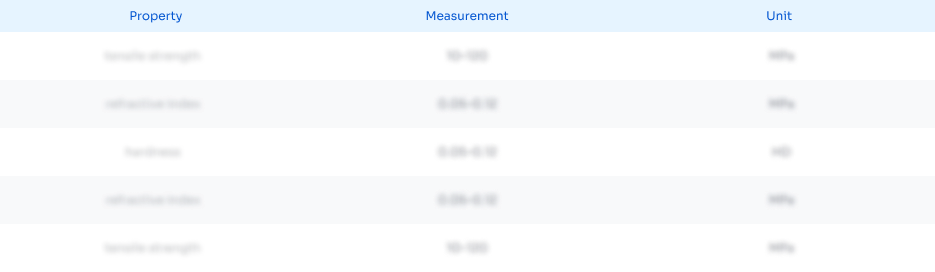
Abstract
Description
Claims
Application Information

- Generate Ideas
- Intellectual Property
- Life Sciences
- Materials
- Tech Scout
- Unparalleled Data Quality
- Higher Quality Content
- 60% Fewer Hallucinations
Browse by: Latest US Patents, China's latest patents, Technical Efficacy Thesaurus, Application Domain, Technology Topic, Popular Technical Reports.
© 2025 PatSnap. All rights reserved.Legal|Privacy policy|Modern Slavery Act Transparency Statement|Sitemap|About US| Contact US: help@patsnap.com