Marine-corrosion-resisting and wear-resisting material, coating and preparation method thereof
A wear-resistant and marine technology, applied in metal material coating technology, coating, metal processing equipment, etc., can solve the problems of coating and substrate galvanic corrosion, coating peeling, etc., and achieve the effect of wide application prospects
- Summary
- Abstract
- Description
- Claims
- Application Information
AI Technical Summary
Problems solved by technology
Method used
Examples
Embodiment 1
[0017] Step 1: using a vacuum atomization process to prepare CuAl alloy powder, wherein the Al content is 0.1-7.4%;
[0018] Step 2: Mechanically mix the CuAl alloy powder prepared in Step 1 with the polyphenylene powder at a weight ratio of 9:1 to obtain an abradable surface layer powder;
[0019] Step 3: Clean the surface of the substrate to be coated and roughen it by blasting sand, screen the CuAl powder prepared in step 1 below 400 mesh, and use the Impact cold spray gun to prepare the CuAl bottom layer. The cold spray parameters are: spray distance 20mm, nitrogen pressure 40bar , The powder feeding rate is 30g / min, the gas temperature is 450°C, and the coating thickness is 0.1-0.2mm.
[0020] Step 4: On top of the cold-sprayed CuAl bottom layer, use atmospheric plasma spraying to spray the abradable surface layer powder prepared in Step 2. The spraying parameters are: current 400A, voltage 70V, powder feeding rate 40g / min, spray distance 120mm, coating thickness 1.5 ~2m...
Embodiment 2
[0022] Step 1: using a vacuum atomization process to prepare CuAl alloy powder, wherein the Al content is 0.1-7.4%;
[0023] Step 2: Mechanically mix the CuAl alloy powder prepared in Step 1 with the polyphenylene ester powder at a weight ratio of 9:1, heat a polyvinyl alcohol binder with a total material weight of 3% in the mixture for agglomeration and granulation, and obtain an abradable surface powder;
[0024] Step 3: Clean the surface of the substrate to be coated and roughen it by blasting sand, screen the CuAl powder prepared in step 1 below 400 mesh, and use the Impact cold spray gun to prepare the CuAl bottom layer. The cold spray parameters are: spray distance 20mm, nitrogen pressure 40bar , The powder feeding rate is 30g / min, the gas temperature is 450°C, and the coating thickness is 0.1-0.2mm.
[0025] Step 4: On top of the cold-sprayed CuAl bottom layer, use atmospheric plasma spraying to spray the abradable surface layer powder prepared in Step 2. The spraying ...
Embodiment 3
[0028] Step 1: using a vacuum atomization process to prepare CuAl alloy powder, wherein the Al content is 0.1-7.4%;
[0029] Step 2: Mechanically mix the CuAl alloy powder prepared in Step 1 with polyphenylene ester powder and hexagonal boron nitride powder in a weight ratio of 8:1:1, and heat a polyvinyl alcohol binder with a total material weight of 3% in the mixture Carry out agglomeration and granulation to obtain abradable surface layer powder;
[0030] Step 3: Clean the surface of the substrate to be coated and roughen it by sand blasting, screen the CuAl powder prepared in step 1 with a mesh size below 500, and use Impact cold spray gun to prepare the CuAl bottom layer. The cold spray parameters are: spray distance 20mm, nitrogen pressure 40bar , The powder feeding rate is 30g / min, the gas temperature is 450°C, and the coating thickness is 0.1-0.2mm.
[0031] Step 4: On top of the cold-sprayed CuAl bottom layer, use atmospheric plasma spraying to spray the abradable su...
PUM
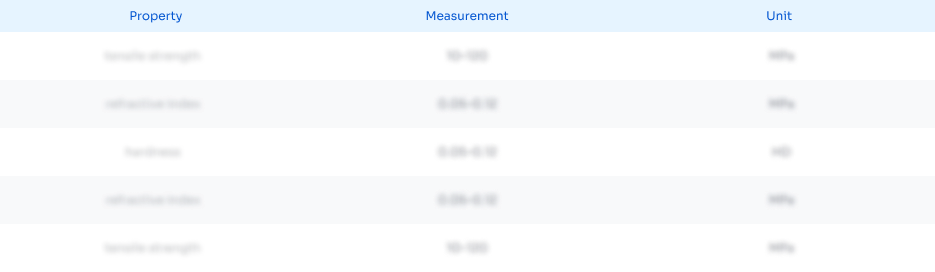
Abstract
Description
Claims
Application Information

- Generate Ideas
- Intellectual Property
- Life Sciences
- Materials
- Tech Scout
- Unparalleled Data Quality
- Higher Quality Content
- 60% Fewer Hallucinations
Browse by: Latest US Patents, China's latest patents, Technical Efficacy Thesaurus, Application Domain, Technology Topic, Popular Technical Reports.
© 2025 PatSnap. All rights reserved.Legal|Privacy policy|Modern Slavery Act Transparency Statement|Sitemap|About US| Contact US: help@patsnap.com