Slab molten steel refining method and steel plate smelting method
A molten steel and slab technology, which is applied in the refining method of slab molten steel and the field of steel plate smelting, can solve the problem that the slab molten steel cannot be poured directly into continuous casting, and achieve the effects of reducing production costs and promoting melting
- Summary
- Abstract
- Description
- Claims
- Application Information
AI Technical Summary
Problems solved by technology
Method used
Image
Examples
Embodiment 1
[0063] This embodiment provides a slab molten steel refining method and a steel plate smelting method, specifically Q235B steel, including:
[0064] The component control requirements of the finished product are: C: 0.13-0.17wt%, Si: 0.12-0.35wt%, Mn: 0.40-0.60wt%, P: ≤0.030wt%, S: ≤0.030wt%. The tapping capacity of the converter is 120 tons.
[0065] 1. The carbon content at the end point of the converter is 0.08wt%, and the added amount of aluminum and iron is calculated according to the relational formula (1). Between 10-20 tons of steel is tapped from the converter, 196kg of aluminum-iron and silicon-manganese and other alloys are added, and the amount of silicon-manganese and other alloys is determined by the composition of the finished product. 400kg of lime is added between 30-40 tons of converter tapping, 70kg of high-alumina slag is added between 90-120 tons of converter, and 7ppm of oxygen is fixed in the argon station. During the tapping process of the converter, ...
Embodiment 2
[0070] This embodiment provides a slab molten steel refining method and a steel plate smelting method, specifically ship plate B steel, including:
[0071] The component control requirements of the finished product are: C: 0.14-0.18wt%, Si: 0.12-0.30wt%, Mn: 0.60-0.90wt%, P: ≤0.028wt%, S: ≤0.023wt%, Als: 0.015-0.030wt% %. The tapping capacity of the converter is 120 tons.
[0072] 1. The carbon content at the end point of the converter is 0.06wt%, and the added amount of aluminum and iron is calculated according to the relational formula (1). Between 10-20 tons of converter tapping, 245kg of aluminum-iron and silicon-manganese alloys are added, between 30-40 tons of tapping, 400kg of lime is added, between 90-120 tons of high-alumina slag, 70kg of high-alumina slag is added, and the oxygen is fixed at 5ppm in an argon station. During the tapping process of the converter, the argon blowing flow rate is 40NM 3 / h.
[0073] 2. The exposed diameter of molten steel is 40cm, and...
Embodiment 3
[0077] This embodiment provides a slab molten steel refining method and a steel plate smelting method, specifically Q345B steel, including:
[0078] The component control requirements of the finished product are: C: 0.14-0.18wt%, Si: 0.15-0.40wt%, Mn: 1.40-1.60wt%, P: ≤0.028wt%, S: ≤0.025wt%, Als: 0.010-0.040wt% %. The tapping capacity of the converter is 120 tons.
[0079] 1. The carbon content at the end point of the converter is 0.04wt%, and the amount of aluminum and iron added is calculated according to the relational formula (1). Between 10-20 tons of steel from the converter, 337kg of aluminum-iron and silicon-manganese alloys are added, between 30-40 tons of steel, 400kg of lime is added, between 90-120 tons of steel, 100kg of high-alumina slag is added, and the oxygen is fixed at 5ppm in an argon station. During the tapping process of the converter, the argon blowing flow rate is 50NM 3 / h.
[0080] 2. The exposed diameter of molten steel is 35cm, and the argon bl...
PUM
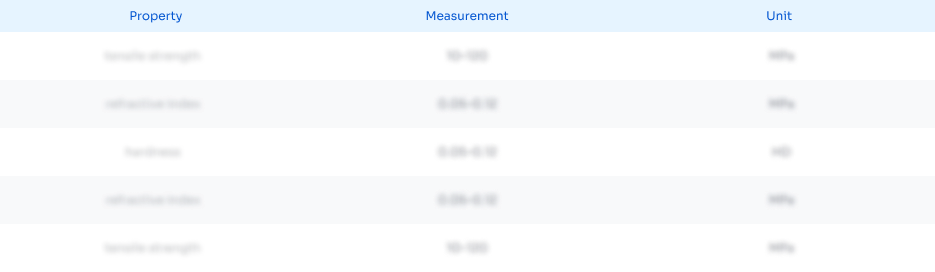
Abstract
Description
Claims
Application Information

- R&D Engineer
- R&D Manager
- IP Professional
- Industry Leading Data Capabilities
- Powerful AI technology
- Patent DNA Extraction
Browse by: Latest US Patents, China's latest patents, Technical Efficacy Thesaurus, Application Domain, Technology Topic, Popular Technical Reports.
© 2024 PatSnap. All rights reserved.Legal|Privacy policy|Modern Slavery Act Transparency Statement|Sitemap|About US| Contact US: help@patsnap.com