Composite dry granules for ceramic tile production and ceramic tile
A ceramic tile and dry grain technology, applied in the field of ceramic tile production, can solve the problems of weak decoration level, inaccurate alignment, and no change in monotony.
- Summary
- Abstract
- Description
- Claims
- Application Information
AI Technical Summary
Problems solved by technology
Method used
Image
Examples
Embodiment 1
[0031] A kind of composite dry granule for the production of ceramic tiles, wherein SiO 2 49.49%, Al 2 o 3 14%, Fe 2 o 3 0.3%, TiO 2 0.01%, CaO 14%, MgO 6%, K 2 O 1%, Na 2 O 1.2%, B 2 o 3 2%, ZrO 2 4%, BaO 2%, F 2%, NiO 2 4%.
[0032] A kind of ceramic brick, described composite dry particle is applied to manufacture ceramic brick, and the method for described manufacture comprises:
[0033] S11. pour glaze in the adobe to obtain glazed surface;
[0034] S12. Applying patterns on the glaze surface;
[0035] S13. Spray glue on the surface of the pattern by an inkjet machine;
[0036] S14. according to the color of the pattern under the glue, the dry granules of a certain color are sprayed onto the glue by the dry granulator;
[0037] S15. Ceramic tiles are obtained after sintering and polishing. In the step S14, it also includes:
[0038] S141. Obtain the pattern under the glue, process the pattern, and obtain the comprehensive color feature and shape fea...
Embodiment 2
[0042] A composite dry particle for ceramic tile production, comprising: SiO 2 45.48%, Al 2 o 3 15%, Fe 2 o 3 0.5%, TiO 2 0.02%, CaO 15%, MgO 7%, K 2 O 1.5%, Na 2 O 1.5%, B 2 o 3 4%, ZrO 2 5%, BaO 1%, F 1%, NiO 2 3%.
[0043] A kind of ceramic tile, described composite dry particle is applied to produce and manufacture ceramic tile, and the method for described manufacture comprises:
[0044] S11. pour glaze in the adobe to obtain glazed surface;
[0045] S12. Applying patterns on the glaze surface;
[0046] S13. Spray glue on the pattern surface;
[0047] S14. Spray dry particles of a certain color onto the glue according to the color of the pattern under the glue;
[0048] S15. Ceramic tiles are obtained after sintering and polishing. The glue is sprayed by an inkjet machine. The dry granules are sprayed by a dry granulator. In the step S141, the processing of the pattern includes grayscale processing and filtering and denoising processing. The polis...
Embodiment 3
[0050] A composite dry particle for ceramic tile production, comprising: SiO 2 50.3%, Al 2 o 3 13%, Fe 2 o 3 0.2%, CaO 12%, MgO5%, K 2 O 0.5%, Na 2 O 1%, B 2 o 3 1%, ZrO 2 3%, BaO 5%, F 4%, NiO 2 5%.
[0051] A kind of ceramic brick, described composite dry particle is applied to manufacture ceramic brick, and the method for described manufacture comprises:
[0052] S11. pour glaze in the adobe to obtain glazed surface;
[0053] S12. Applying patterns on the glaze surface;
[0054] S13. Spray glue on the pattern surface;
[0055] S14. Spray dry particles of a certain color onto the glue according to the color of the pattern under the glue;
[0056] S15. Ceramic tiles are obtained after sintering and polishing. The glue is sprayed by an inkjet machine. In the step S141, the processing of the pattern includes one of grayscale processing, filtering and denoising processing, and normalization processing. The polishing method is DP fine polishing.
PUM
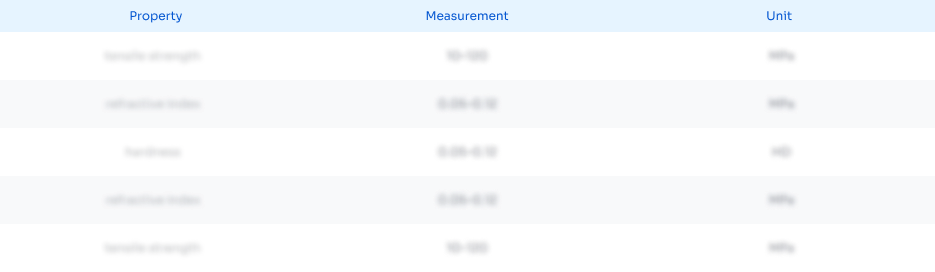
Abstract
Description
Claims
Application Information

- R&D
- Intellectual Property
- Life Sciences
- Materials
- Tech Scout
- Unparalleled Data Quality
- Higher Quality Content
- 60% Fewer Hallucinations
Browse by: Latest US Patents, China's latest patents, Technical Efficacy Thesaurus, Application Domain, Technology Topic, Popular Technical Reports.
© 2025 PatSnap. All rights reserved.Legal|Privacy policy|Modern Slavery Act Transparency Statement|Sitemap|About US| Contact US: help@patsnap.com